标准规范下载简介和预览
在线阅读
中华人民共和国城镇建设行业标准
城市轨道交通桥梁盆式支座
Pot bearings for urban rail transit bridges
CJ/T 464-2014
发布部门:中华人民共和国住房和城乡建设部
发布日期:2014年10月20日
实施日期:2015年04月01日
前 言
本标准按照GB/T 1.1-2009给出的规则起草。
本标准由住房和城乡建设部标准定额研究所提出。
本标准由住房和城乡建设部城市轨道交通标准化技术委员会归口。
本标准负责起草单位:衡水宝力工程橡胶有限公司
本标准参加起草单位:北京城建设计研究总院有限责任公司
国家工程橡胶产品质量监督检验中心
上海市城市建设设计研究总院
中交第一公路勘察设计研究院有限公司
中铁第一勘察设计院集团有限公司
海口市市政工程设计研究院
河北省工程橡胶工程技术研究中心
本标准主要起草人:王希慧 刘欣顺 赵九平 阙孜 张晓林 李红 彭俊 高山 王伟 杨少军 吴延伟 周师凯
1 范围
本标准规定了城市轨道交通桥梁盆式支座的规格、分类、型号、产品组成结构,材料,要求,试验方法,检验规则,标志、包装、运输和贮存等要求。
本标准适用于竖向设计承载力为500kN~100 000kN、抗震设防烈度为8度以下(含8度)地区的城市轨道交通桥梁和道路桥梁用盆式支座,不适用于磁悬浮轨道交通和跨座式单轨轨道交通桥梁用支座。
2 规范性引用文件
下列文件对于本文件的应用是必不可少的。凡是注日期的引用文件,仅注日期的版本适用于本文件。凡是不注日期的引用文件,其最新版本(包括所有的修改单)适用于本文件。
GB/T 528 硫化橡胶或热塑性橡胶 拉伸应力应变性能的测定
GB/T 1033.1 塑料 非泡沫塑料密度的测定 第1部分:浸渍法、液体比重瓶法和滴定法
GB/T 1040.2 塑料 拉伸性能的测定 第2部分:模塑和挤塑塑料的试验条件
GB/T 1591 低合金高强度结构钢
GB/T 1682 硫化橡胶低温脆性的测定 单试样法
GB/T 2040 铜及铜合金板材
GB/T 3280 不锈钢冷轧钢板和钢带
GB/T 3398.1 塑料 硬度测定 第1部分:球压痕法
GB/T 3512 硫化橡胶或热塑性橡胶 热空气加速老化和耐热试验
GB/T 4171 耐候结构钢
GB/T 6031 硫化橡胶或热塑性橡胶硬度的测定(10~100 IRHD)
GB/T 7759 硫化橡胶、热塑性橡胶 常温、高温和低温下压缩永久变形测定
GB/T 7762 硫化橡胶或热塑性橡胶 耐臭氧龟裂 静态拉伸试验
GB 50661 钢结构焊接规范
HG/T 2366 二甲基硅油
HG/T 2502 5201硅脂
TB/T 2331 铁路桥梁盆式支座
3 术语和定义
3.1
调高盆式支座 height adjustable pot bearing
通过设置在盆式支座下支座板上的填充孔道,向支座钢盆内注入合成材料,实现无级调高功能的支座。
3.2
改性聚四氟乙烯 modified polytetrafluoroethylene plate
通过改变聚四氟乙烯的分子链结构,获得的高压(45MPa)下具有低摩擦系数、耐磨耗和高温、压缩稳定的非金属材料。
.
4 规格、分类、型号、产品组成结构
4.1 规格
4.1.2 固定盆式支座水平各向、纵向活动盆式支座横桥向、横向活动盆式支座顺桥向的设计水平荷载分为六级:0.1P、0.15P、0.2P、0.25P、0.3P、0.4P,P为支座的竖向设计承载力。
4.1.3 多向活动盆式支座和纵向活动盆式支座的顺桥向位移分为六级:±50mm、±100mm、±150mm、±200mm、±250mm和±300mm;多向活动盆式支座和横向活动盆式支座的横桥向位移分为四级:±10mm、±20mm、±30mm和±40mm。
4.1.4 调高盆式支座调高量为0mm~30mm。
4.2 分类
4.2.1 按使用功能分为:
a) 普通盆式支座,代号:P;
b) 调高盆式支座,代号:T。
4.2.2 按使用性能分为:
a) 固定盆式支座,承受竖向荷载和各向水平荷载,具有竖向转动性能,代号:GD;
b) 纵向活动盆式支座,承受竖向荷载和横桥向水平荷载,具有竖向转动及顺桥向位移性能,代号:ZX;
c) 横向活动盆式支座,承受竖向荷载和顺桥向水平荷载,具有竖向转动及横桥向位移性能,代号:HX;
d) 多向活动盆式支座,承受竖向荷载,具有竖向转动和水平多向位移性能,代号:DX。
4.2.3 按适用纵向坡度分为:
a) 支座顶面不设坡度,适用于线路坡度0≤i≤4‰,代号:i0;
b) 支座顶面预设8‰坡度,适用于线路坡度4‰<i≤12‰,代号:i8;
c) 支座顶面预设16‰坡度,适用于线路坡度12‰<i≤20‰,代号:i16;
d) 支座顶面按i的实际值预设坡度,适用于线路坡度20‰<i≤30‰,代号:iXX。
4.2.4 按适用温度范围分为:
a) 常温型支座,适用于-25℃~+60℃,代号:C;
b) 耐寒型支座,适用于-40℃~+60℃,代号:F。
4.3 型号
图1 城市轨道交通桥梁盆式支座型号表示方法
示例1:
普通型、设计竖向承载力1500kN、各向设计水平荷载为竖向设计承载力的10%、支座顶面纵向坡度4‰、常温型固定盆式支座,其型号表示为:CJPZ-P1500 GD-0.1P-i0-C。
示例2:
普通型、设计竖向承载力2000kN、顺桥向位移量±100mm、横桥向设计水平荷载为竖向设计承载力的15%、支座顶面纵向坡度8‰、耐寒型纵向活动盆式支座,其型号表示为:CJPZ-P2000 ZX-e±100-0.15P-i8-F。
示例3:
调高型、设计竖向承载力3000kN、顺桥向位移量±100mm、横桥向位移量±10mm、调高量20mm、支座顶面纵向坡度27‰、耐寒型多向活动盆式支座,其型号表示为:CJPZ-T3000 DX-e±100/±10-(20)-i27-F。
4.4 产品组成结构
4.4.1 固定普通盆式支座由上支座板、橡胶承压板、锚固螺栓、套筒、下支座板、橡胶密封圈、黄铜密封圈和防尘围板等零部件组成,结构示意见图2a)。
4.4.2 纵向活动普通盆式支座和横向活动普通盆式支座由上支座板、不锈钢板、改性聚四氟乙烯板、中间钢衬板、橡胶承压板、SF-ⅠB三层复合板、锚固螺栓、套筒、下支座板、橡胶密封圈、黄铜密封圈和防尘围板等零部件组成,结构示意见图2b)、图2c)。
4.4.3 多向活动普通盆式支座由上支座板、不锈钢板、改性聚四氟乙烯板、中间钢衬板、橡胶承压板、锚固螺栓、套筒、下支座板、橡胶密封圈、黄铜密封圈和防尘围板等零部件组成,结构示意见图2d)。
4.4.4 固定调高盆式支座由上支座板、橡胶承压板、锚固螺栓、套筒、合成材料、下支座板、橡胶密封圈、黄铜密封圈、填充孔道、丝堵和防尘围板等零部件组成,结构示意见图2e)。
4.4.5 纵向活动调高盆式支座和横向活动调高盆式支座由上支座板、不锈钢板、改性聚四氟乙烯板、中间钢衬板、橡胶承压板、SF-ⅠB三层复合板、锚固螺栓、套筒、合成材料、下支座板、橡胶密封圈、黄铜密封圈、填充孔道、丝堵和防尘围板等零部件组成,结构示意见图2f)、图2g)。
4.4.6 多向活动调高盆式支座由上支座板、不锈钢板、改性聚四氟乙烯板、中间钢衬板、橡胶承压板、锚固螺栓、套筒、合成材料、下支座板、橡胶密封圈、黄铜密封圈、填充孔道、丝堵和防尘围板等零部件组成,结构示意见图2h)。
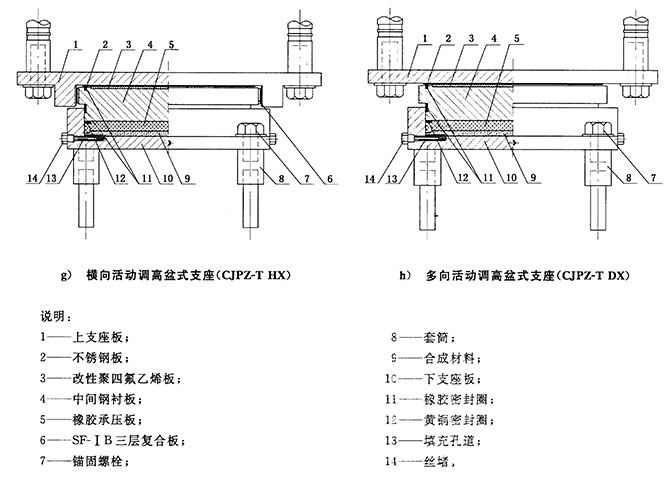
图2 支座结构示意(防尘围板未示出)
.
5 材料
5.1 支座用材的物理、化学性能
5.1.1 橡胶
橡胶物理机械性能及各项指标的测定方法应符合TB/T 2331的规定。
5.1.2 合成材料
合成材料应经检验合格后方可进厂。合成材料的标识和包装应完整,物理机械性能应符合表1的要求。合成材料试样制备应按附录A进行。
表1 合成材料物理机械性能
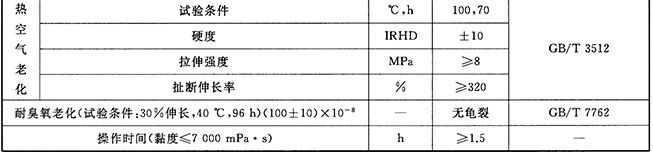
5.1.3 改性聚四氟乙烯板
5.1.3.1 改性聚四氟乙烯板物理机械性能应符合表2的要求。摩擦系数与线磨耗率试验方法应按附录B进行。
表2 改性聚四氟乙烯板物理机械性能
5.1.3.2 改性聚四氟乙烯板在5201-2硅脂润滑条件下,与不锈钢板间的摩擦系数,在平均压应力45MPa时,应符合表3的要求;在相对滑动速度15mm/s(正弦波0.375Hz),往复滑动距离±10mm,累计滑动距离50km时,线磨耗率不应大于5μm/km。
表3 改性聚四氟乙烯板摩擦系数
5.1.3.3 改性聚四氟乙烯板在无硅脂润滑条件下,与不锈钢板间的摩擦系数和线磨耗率,在平均压应力45MPa时,应符合以下要求:
a) 常温(23℃±2℃)时,在相对滑动速度15mm/s(正弦波0.375Hz)、往复滑动距离±10mm、累计滑动距离1km时,线磨耗率不应大于200μm/km,磨耗过程中动摩擦系数不应大于0.07;
b) 高温(60℃±2℃)时,累计滑动距离1km时,线磨耗率不应大于180μm/km,动摩擦系数不应大于0.06。
5.1.4 硅脂
5201-2硅脂的物理性能及各项指标的测定方法应符合HG/T 2502的规定。
5.1.5 粘接剂
改性聚四氟乙烯板与钢板粘结,应采用不可溶和热固性的粘结剂,剥离粘合强度不应小于5kN/m。
5.1.6 钢件
5.1.6.1 上支座板、中间钢衬板、下支座板的材料采用Q345B(严寒地区采用Q345D)热轧钢板或锻件,化学成分和力学性能应符合GB/T 1591的规定;处于高湿度、高盐度等严重腐蚀环境,宜采用Q355NH热轧钢板或锻件,化学成分和力学性能应符合GB/T 4171的规定。
5.1.6.2 铸钢件化学成分、热处理后的机械性能(含冲击功Akv)及内在质量等均应符合TB/T 2331的规定。
5.1.6.3 锚固螺栓材料化学成分和力学性能应符合TB/T 2331的规定。
5.1.7 不锈钢板
不锈钢板采用镜面精轧不锈钢冷轧钢板,采用牌号、化学成分及力学性能应符合TB/T 2331的规定。
5.1.8 黄铜
黄铜密封圈应采用H62牌号黄铜,化学成分和力学性能应符合GB/T 2040的规定。
5.1.9 SF-ⅠB三层复合板
纵向和横向活动盆式支座的中间钢衬板侧向导向滑条应采用SF-ⅠB三层复合板,成分、层间结合牢度、压缩永久变形、初始静摩擦系数及层间结合牢度、压缩永久变形、初始静摩擦系数的测定方法应符合TB/T 2331的规定。
5.2 支座用材的尺寸与偏差
5.2.1 橡胶承压板
橡胶承压板直径和厚度偏差应符合TB/T 2331的规定。
5.2.2 改性聚四氟乙烯板
5.2.2.1 改性聚四氟乙烯板可采用整体板或拼接板,基准厚度t为7mm~8mm,嵌入深度不应小于基准厚度1/2,外露高度不应小于3mm,尺寸及装配间隙偏差应符合表4的要求。
表4 改性聚四氟乙烯板尺寸及装配间隙偏差 单位为毫米
5.2.2.2 改性聚四氟乙烯板若采用中心圆盘与周边环带组合时,中心圆盘直径不应小于1000mm,环带宽度不应小于50mm,环带最多可分为四等份。
5.2.2.3 改性聚四氟乙烯板滑动面上应设有驻留5201-2硅脂的储脂槽,储脂槽应采用热压成型,不应用机械方法成型。储脂槽的平面尺寸及布置应符合图3的要求。
图3 改性聚四氟乙烯板储脂槽的平面尺寸及布置
5.2.2.4 改性聚四氟乙烯板模压表面平面度公差:当直径d≤670mm时,不应大于0.2mm,当直径d>670mm时,不应大于0.0003d。
5.2.3 不锈钢板
不锈钢板表面应符合GB/T 3280中8号表面加工要求,表面粗糙度Ra不应大于0.8μm。不锈钢板与基层钢板采用氩弧周边连续焊接,焊接后应与基层钢板密贴。不锈钢板厚度及焊接后的平面度最大偏差应符合表5的要求。焊缝应光滑、平整、连续、焊接要求应符合GB 50661中一级的规定。
表5 不锈钢板厚度与尺寸偏差 单位为毫米
5.2.4 黄铜密封圈
黄铜密封圈的组成、布置方式、密封铜环的截面尺寸、数量及切口角度应符合TB/T 2331的规定。
5.2.5 SF-ⅠB三层复合板
SF-ⅠB三层复合板用材规格应符合TB/T 2331的规定。
5.2.6 加工
机加工件的尺寸公差、焊接部位的技术要求及铸钢件的缺陷焊补应符合TB/T 2331的规定。
5.3 支座用材的外观质量
5.3.2 改性聚四氟乙烯板
改性聚四氟乙烯板外观应符合表6的要求。
表6 改性聚四氟乙烯板外观要求
5.4 支座用材的检验
原材料进厂应首先检查产品合格证,检验项目、检验内容、要求、检验频次应符合表7的规定。
表7 原材料进厂检验

.
6 要求
6.1 支座性能要求
在竖向设计承载力作用下,支座竖向压缩变形不应大于支座总高度的2%,下支座板盆环外侧上口处径向变形不应大于盆环外径的0.05%。
6.1.2 水平变形
在设计水平荷载作用后,支座水平方向残余变形不应大于整个加载过程中水平方向弹性变形的5%。
6.1.3 竖向转角
支座竖向设计转角不应小于0.02rad。
6.1.4 摩擦系数
6.1.4.1 不加硅脂润滑时,活动支座设计摩擦系数常温时不应大于0.07,高温时不应大于0.06。
6.1.4.2 加5201-2硅脂润滑后,常温型活动支座设计摩擦系数不应大于0.03,耐寒型活动支座设计摩擦系数不应大于0.05。
6.1.5 调高盆式支座要求
6.1.5.1 调高盆式支座在填充及使用过程中应密封良好,合成材料应无渗漏,填充孔道应无堵塞。
6.1.5.2 调高盆式支座下支座板应符合以下要求:
a) 下支座板盆腔底部至少设置四道合成材料注入盆腔底部的填充孔道。下支座板盆腔深度应满足在最大调高量和最大竖向转角的条件下,固定支座上座板和纵向、横向及多向活动支座中间钢衬板的凸缘顶面与下支座板盆腔顶面的距离不小于5mm,并应满足多次无级调高的需要。以固定调高盆式支座为例,见图4;
b) 下支座板的圆形盆腔底板厚度应满足合成材料填充孔道和竖向承载力的要求。
图4 固定调高盆式支座最大转角示意
6.1.6 密封性
调高盆式支座橡胶承压板应设置防止合成材料乳状液体泄露的密封结构,在荷载下不应发生泄漏。
6.2 支座防腐与防尘
支座的防腐与防尘应符合TB/T 2331的规定。
6.3 组装
6.3.2 调高盆式支座组装应符合6.3.1的要求,在装配时应对合成材料填充孔道的螺纹部位和丝堵涂抹硅脂,丝堵安装要紧固。
6.4 特殊设计
6.5 疲劳性能试验
成品支座应进行竖向承载的200万次疲劳性能试验,试验后拆开支座观察,允许有少量粉末从盆环内挤出,橡胶承压板、黄铜密封圈和钢盆各部件应无明显破坏现象,调高盆式支座不应有合成材料泄漏现象。
7 试验方法
7.2 调高盆式支座调高密封性能试验按附录E进行。
7.3 成品支座竖向承载的200万次疲劳性能试验按附录F进行。
7.4 成品支座的竖向承载力、摩擦系数、转动性能、转动磨耗试验应按TB/T 2331的规定进行。
.
8 检验规则
8.1 检验分类
8.1.2 出厂检验为支座生产厂在每批产品交货前进行的检验。
8.1.3 型式检验应由具有相应资质的质量检测机构进行。有下列情况之一时,应进行型式检验:
a) 新产品定型生产时;
b) 结构、材料、工艺等有重大改变,可能影响产品性能时;
c) 正常生产每三年时;
d) 产品停产两年后,恢复生产时;
e) 出厂检验结果与上次型式检验有较大差异时。
8.2 检验内容
表8 出厂检验、型式检验
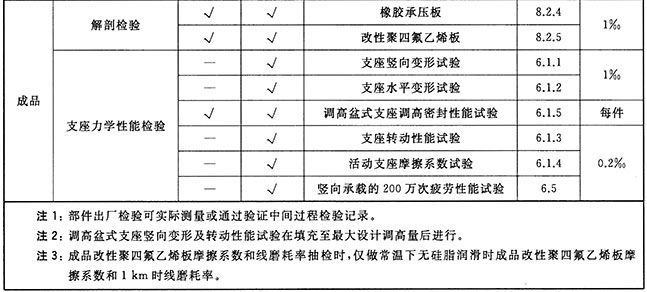
8.2.2 成品支座试验应在经国家计量认证的试验检测机构进行,条件许可时也可在支座生产厂进行。
8.2.3 成品支座竖向变形、水平变形、调高盆式支座调高密封性能、转动性能、活动支座摩擦系数和竖向承载的200万次疲劳性能试验采用随机抽样的方式,应符合表8中的要求。成品支座当受试验设备能力限制时,可选用有代表性的竖向设计承载力小的支座进行试验,支座竖向设计承载力不应小于2000kN。
8.2.4 成品支座橡胶承压板的解剖试验按TB/T 2331的规定进行。
8.2.5 成品支座改性聚四氟乙烯板的解剖试验应在厂家成品库或运至现场的产品中任取一块改性聚四氟乙烯板,测定其密度、拉伸强度、断裂伸长率、球压痕硬度及压缩变形量,检验结果应符合5.1.3.1的要求。
8.3 检验结果的判定
9 标志、包装、运输和贮存
附 录 A
(规范性附录)
合成材料试样制备
A.1 取样方法
按一定比例分别从A料桶、B料桶中取A料和B料,放于三口烧瓶中。
注:合成材料为双组分高分子化合物。在实际应用中两个液态组分通过搅拌混合转化为弹性固体,两个液态组分为A料和B料。
A.2 试样制备
A.2.1 称取一定量的A料于三口烧瓶中,安装温度计、电动搅拌器、升温至80℃±5℃,在此温度下搅拌抽真空脱泡30min~40min。
A.2.2 卸去真空后,将A料自然冷却至45℃~50℃,按比例加入一定量B料,保持温度在50℃~60℃时,搅拌抽真空脱泡20min~30min。
A.2.3 将混合好的A料、B料,倒入已预热并涂有硅脂的模具中,在110℃下加热硫化30min~40min,脱模,在100℃~110℃烘箱中后硫化24h,取得拉伸性能和恒定压缩永久变形用试样。
A.2.4 拉伸性能试样采用l型哑铃状,试样厚度保持在2mm±0.2mm。恒定压缩永久变形试样采用A型,试样直径为29mm±0.5mm,高12.5mm±0.5mm的圆柱体。
附 录 B
(规范性附录)
改性聚四氟乙烯板摩擦系数与线磨耗率试验方法
B.1 试样
改性聚四氟乙烯板摩擦系数与线磨耗率试验用试件尺寸见图B.1。对磨件不锈钢板长140mm,宽110mm,厚2mm。不锈钢板四周焊接在厚约15mm的基层钢板上,要求焊缝光滑、平整,焊缝不高出不锈钢板表面。不锈钢板的表面和外观质量应符合5.2.3、5.3.1的要求。
图B.1 改性聚四氟乙烯板摩擦系数试验试件
B.2 试样数量
摩擦系数和线磨耗率试样数量均为3组,取3组试件测试平均值为该批改性聚四氟乙烯板摩擦系数和线磨耗率的测试结果。
B.3 试验方法
B.3.1 摩擦系数试验应包含以下内容:
a) 改性聚四氟乙烯板摩擦系数测试采用双剪试验方法,试验装置见图B.2。试验分为有硅脂润滑试验和无硅脂润滑试验,有硅脂润滑试验时将试件储脂槽内涂满5201-2硅脂。常温试验温度为23℃±2℃,低温试验温度为-35℃±2℃,高温试验温度为60℃±2℃。试验前先对试件进行预压,预压时间为1h,试件压应力为45MPa。
b) 在相对滑动速度0.4mm/s(正弦波0.01Hz),往复滑动距离为±10mm,连续5次循环过程中摩擦系数的平均值为该批改性聚四氟乙烯板的静摩擦系数。在相对滑动速度15mm/s(正弦波0.375Hz),往复滑动距离为±10mm,连续10次循环过程中摩擦系数的平均值为该批改性聚四氟乙烯板的动摩擦系数。
c) 一般情况下,只做常温试验,当有特殊要求时再做低温试验和高温试验。实验前应将试件在试验温度下停放24h,以使试件内外温度一致。
B.3.2 线磨耗率试验应包含以下内容:
a) 改性聚四氟乙烯板线磨耗率测试采用双剪试验方法,试验装置见图B.2。试验分为有硅脂润滑试验和无硅脂润滑试验,有硅脂润滑试验时将试件储脂槽内涂满5201-2硅脂。常温试验温度为23℃±2℃,高温试验温度为60℃±2℃。试验前先对试件进行预压,预压时间为1h,试件压应力为45MPa。在相对滑动速度15mm/s(正弦波0.375Hz),相对往复滑动距离为±10mm,累计滑动距离50km(型式检验)。现场抽检时仅做1km无硅脂润滑下线磨耗率试验。
b) 线磨耗率由试验前后试件重量损失计算确定。
B.4 试验报告
试验报告应包含以下内容:
a) 试验概况:包括试验设备、试验荷载、试验温度、加载速度等;
b) 试验过程有无异常情况,如有异常,描述异常发生的过程;
c) 试件摩擦系数实测结果,并评定试验结果;
d) 试件线磨耗率实测结果,并评定试验结果;
e) 试验现场照片。
附 录 C
(规范性附录)
改性聚四氟乙烯板荷载压缩变形试验方法
C.1 试样
改性聚四氟乙烯板荷载压缩变形试验用试样直径为155mm,板厚7mm,外露高度3mm。改性聚四氟乙烯板储脂坑内涂满5201-2硅脂。
C.2 试验数量
改性聚四氟乙烯板荷载压缩变形试样数量为3组。
C.3 试验方法
试验开始前,在常温23℃±2℃条件下用4个千分尺在改性聚四氟乙烯板表面选取对称4点作为测量点,并以4个千分尺测量结果的平均值作为改性聚四氟乙烯板的初始外露高度h0。在整个试验过程中应保持荷载和温度的稳定,连续测量并记录外露高度的变化。
试验时,试样加热至35℃±2℃,保持1h,然后加压至90MPa,用4个千分表连续记录改性聚四氟乙烯板外露高度随时间的变化值,直至48h。外露高度随时间的变化值(△h)按式(C.1)进行计算:
外露高度随时间的变化值(△h)符合式(C.2)的要求时,可确认改性聚四氟乙烯板变形已经稳定。
式中:
△h——外露高度随时间的变化值(mm);
hε——外露高度变量值(mm);
h48——48h时外露高度(mm);
ε——时间变量值(h);
h0——初始外露高度(mm)。
C.4 试验报告
试验报告应包括以下内容:
a) △h和时间的关系曲线;
b) 温度和时间的关系曲线;
c) 改性聚四氟乙烯板变形稳定性判定;
d) 试验照片。
附 录 D
(规范性附录)
成品支座水平荷载试验方法
D.1 试样
试验宜采用实体支座,如受试验设备能力限制时,可选用竖向设计承载力不小于2000kN的支座。试验前将试样直接置于标准温度下23℃±2℃,停放24h。
D.2 试验方法
成品支座水平荷载试验应在专用试验机上进行,试验装置见图D.1。放置试样后,按下列步骤进行支座水平荷载试验:
图D.1 成品支座水平荷载试验装置示意
a) 试样放置:将试样置于试验机的承载板上,将自平衡反力架及水平荷载试验装置组合配置好。如图D.1所示;
b) 安装位移传感器:水平荷载试验试验荷载为支座设计水平荷载的1.2倍,将水平荷载加载至试验荷载的0.5%后,核对水平方向位移传感器(百分表)及水平千斤顶数据。确认无误后,进行预加载;
c) 预加载:支座竖向承载力加至设计承载力的50%持荷后,用试验荷载的20%进行预加载,反复进行3次;
d) 正式加载:将水平荷载由试验荷载的0.5%至试验荷载均匀分为10级;试验时先将竖向承载力加至设计承载力的50%;试验荷载的0.5%作为初始推力,逐级加载,每级荷载稳压2min后,记录百分表数据;待水平荷载达到试验荷载的90%后,再将竖向承载力加至设计承载力。然后,将水平荷载加至试验荷载稳压3min后卸载至初始推力。正式加载过程连续进行3次;
e) 试验结果:水平荷载作用下变形分别取2个百分表的平均值,绘制荷载-水平变形曲线。
D.3 试验报告
试验报告应包括以下内容:
a) 试件概况描述:包括支座型号、竖向设计承载力、水平荷载、转角、位移,并附简图;
b) 试验机性能及配置描述;
c) 实验过程中出现异常现象描述;
d) 试验记录完整,评定试验结果;
e) 附试验照片。
附 录 E
(规范性附录)
调高盆式支座调高密封性能试验方法
E.1 试样
试验宜采用实体支座,如受试验设备能力限制时,可选用竖向设计承载力不小于2000kN的支座。
试验支座的材质应符合第5章的要求,支座各部件及支座外形尺寸应符合设计要求。
E.2 试验内容
在设计荷载作用下,测试支座保压密封性能。
E.3 试验方法
E.3.1 支座调高试验应在专用试验机上进行,并配备调高专用填充材料注入设备,试验用填充材料为二甲基硅油。试验装置见图E.1。试验方法如下。
图E.1 成品支座调高试验装置
a) 将二甲基硅油加入调高设备中,打开阀门3启动调高设备,向支座内注入二甲基硅油;
b) 将支座放置在压力试验机中心位置。开启试验机,首先在空载状态下,将支座调高5mm,关闭阀门3,支座稳压10min后,压力降低不超过0.5MPa。打开支座掀掉中间钢衬板,检查支座铜圈与盆内壁之间有无二甲基硅油漏泄,可判定为密封性能检测合格,如保压时压力降低超过0.5MPa,应检查泄露部位,进行修复后复检;
c) 按序号b)的试验步骤和方法分别在支座上施加设计荷载的50%和100%,检验调高支座的密封性能。
E.3.2 二甲基硅油的性能应符合HG/T 2366的规定。
E.4 试验结果
支座调高试验后,要求支座内压强降低不应超过0.5MPa。
E.5 试验报告
试验报告应包括以下内容:
a) 试验装置及试验概况:试验设备、试验荷载、试验室温度;试验支座型式及规格,试验支座高度;
b) 描述试验结果及试验过程,记录试验过程中的异常情况;
c) 提供支座在荷载加压作用下调高结果,并对试验结果做出评定;
d) 试验照片:包括试验支座持荷及调高过程中的异常情况。
附 录 F
(规范性附录)
成品支座竖向承载的200万次疲劳性能试验方法
试验宜采用实体支座,如受试验设备能力限制时,可选用竖向设计承载力不小于2000kN的支座。调高盆式支座应在调高后进行。
F.2 试样数量
试样选用两件规格型号相同的固定支座。
F.3 试验方法
F.3.1 成品支座竖向承载的200万次疲劳性能试验测定支座的竖向压缩变形,试验在专用试验机上进行,试验机应满足平稳、连续加载,疲劳荷载上限力为支座竖向设计承载力,下限力与上限力比值取0.6。
F.3.2 试验按下列步骤进行:
a) 对中安装好试样后,在每件试验支座上、下支座板间对称放置4只百分表,测试支座竖向压缩变形;
b) 加载试验前,应对支座进行预压,预压荷载为支座竖向设计承载力,预压次数为3次;
c) 正式加载时,试验荷载由零至上限力,然后卸载至下限力,加载频率为2.2Hz。以上加载过程应连续进行200万次。
F.3.3 取4只百分表读数的算术平均值作为竖向压缩变形的实测值,加载20万次记录一次,试验完成后分别绘制两件支座的加载次数-竖向压缩变形曲线。
F.4 试验结果
疲劳试验后,拆开支座观察,允许有少量粉末从盆环内挤出,橡胶承压板、黄铜密封圈和钢盆各部件应无明显破坏现象,调高盆式支座不应有合成材料泄漏现象。
F.5 试验报告
试验报告应包括以下内容:
a) 试验装置及试验概况:试验设备、试验荷载;试验支座规格,试验支座高度;
b) 描述试验结果及试验过程,记录试验过程中的异常情况;
c) 绘制加载次数-竖向压缩变形曲线;
d) 提供支座在200万次竖向荷载加载作用后竖向压缩变形结果,并对试验结果做出评定;
e) 试验照片。