标准规范下载简介
在线阅读
中华人民共和国国家标准
医药工程安全风险评估技术标准
Pharmaceutical engineering technical standard for safety risk assessment
GB/T 51116-2016
主编部门:中国医药工程设计协会
批准部门:中华人民共和国住房和城乡建设部
施行日期:2016年12月1日
中华人民共和国住房和城乡建设部公告
第1089号
住房城乡建设部关于发布国家标准《医药工程安全风险评估技术标准》的公告
本标准由我部标准定额研究所组织中国计划出版社出版发行。
中华人民共和国住房和城乡建设部
2016年4月15日
前言
本标准是根据住房城乡建设部《关于印发<2010年工程建设标准规范制订、修订计划>的通知》(建标[2010]43号文)的要求,由中国医药集团重庆医药设计院会同有关单位编制而成的。
本标准在编制过程中,编制组经广泛调查研究,认真总结实践经验,参考有关国内标准和国外先进标准,并在广泛征求意见的基础上,编制本规范。最后经审查定稿。
本标准共分5章和5个附录。主要内容有:总则、术语、风险评估程序和风险评估阶段、风险分析方法、风险评估等。
本标准由住房城乡建设部负责管理,由中国医药工程设计协会负责日常管理,由中国医药集团重庆医药设计院负责具体技术内容的解释。在本规范执行过程中,如有需要修改和补充之处,请将意见和建议寄交中国医药集团重庆医药设计院(地址:重庆市渝中区大坪正街8号,邮政编码:400042),以供今后修订时参考。
本标准主编单位、参编单位、主要起草人和主要审查人:
主编单位:中国医药集团重庆医药设计院
参编单位:中国石化上海工程有限公司
中国医药集团联合工程有限公司
重庆科技学院安全工程学院
北大方正集团重庆西南合成制药股份有限公司
主要起草人:潘晓勤 谭建国 谢友强 吴霞 程宁 白建平 陈学明 刘炜 徐青云 张洪 伍莉萍 王雪梅 缪晡 赵肖兵 刘启发 蔡治勇 梁中
主要审查人:杨军 张延松 柳静献 罗宁 吴树民 冉蜀英 周永春 王廷春 郝孝铭 刘国勇 张长银 张安明 杨铁荣
1 总 则
1.0.1 为规范医药工业的风险评估,提高评估水平,制定本标准。
1.0.2 本标准适用于新建、改建和扩建的医药工程项目的安全预评价、安全验收评价及投产使用后的安全现状评价,也适用于医药工程的研究开发、设计、维修、拆除退役、事故分析等过程的风险评估。
1.0.3 本标准不适用于生物制品生产、放射性药品生产及医疗器械等医药工程安全风险评估。
1.0.4 医药工程项目的风险评估,除应符合本标准外,尚应符合国家现行有关标准的规定。
2 术 语
2.0.1 危险 hazard
可能造成人员伤害、职业病、财产损失、环境破坏的根源或状态。
2.0.2 危险辨识 hazard identification
采用系统分析方法识别出系统中存在的危险或事故隐患。
2.0.3 安全 safety
免遭不可接受危险的伤害。
2.0.4 系统 system
由若干相互联系的、为了达到一定目标而具有独立功能的要素所构成的有机整体。
2.0.5 事故 accident
造成人员死亡、伤害、职业病、财产损失或其他损失的意外事件。
2.0.6 危险因素 risk factor
对人造成伤亡或对物造成突发性损害的因素。
2.0.7 有害因素 harmful factor
影响人的身体健康,导致疾病,或对物造成慢性损害的因素。
2.0.8 重大危险源 major hazard source
长期地或临时地生产、搬运、使用或者储存危险物品,且危险物品的数量等于或超过临界量的单元(包括场所和设施)。
2.0.9 风险 risk
发生特定危害事件的可能性以及发生事件后果严重性的结合。
2.0.10 风险水平 level of risk
结合事件发生的可能性及其后果表示的风险量值。
2.0.11 风险等级 risk rating
基于风险水平划分的风险级别。
2.0.12 风险准则 risk criteria
评估风险等级时与之对照的参考基准。
2.0.13 风险辨识 risk identification
发现、确认、描述风险的过程。
2.0.14 风险分析 risk analysis
认知风险属性和推断风险水平的过程。
2.0.15 风险评价 risk evaluation
依据风险准则,确定风险等级的过程。
2.0.16 风险评估 risk assessment
风险辨识、风险分析、风险评价的全过程。
2.0.17 安全设施 safety facilities
企业(单位)在生产经营活动中将危险因素、有害因素控制在安全范围内以及预防、减少、消除危害所配备的装置(设备、装备)。
2.0.18 应急电源 electric source for safety services
用作应急供电系统组成部分的电源。
2.0.19 爆炸危险区域 explosion hazardous area
爆炸性混合物出现的或预期可能出现的数量达到足以要求对电气设备的结构、安装和使用采取预防措施的区域。
2.0.20 关键控制点 critical control point(CCP)
可运用控制,并有效防止或消除产品安全危害,或降低到可接受水平的关键步骤。
2.0.21 关键限值 critical threshold value
将可接受水平与不可接受水平区分开的判定标准。
2.0.22 流程图 flow diagram
生产或制作特定产品所用操作顺序的系统表达。
2.0.23 危害分析关键控制点 hazard analysis critical control point(HACCP)
对产品安全有显著意义的危害加以识别、评估以及控制产品安全危害的体系。
.
3 风险评估程序和风险评估阶段
3.1 风险评估程序
3.1.1 医药工程项目风险评估的流程应符合本标准附录A的要求,具体过程应包括下列步骤:
1 熟悉系统,收集数据;
2 基础数据收集及分析;
3 危险、有害因素辨识;
4 风险频率(P)分析;
5 风险后果(S)分析;
6 风险计算[R=f(P,S)];
7 风险标准;
8 风险评估;
9 针对出现的重大风险提出措施,对重大风险再评估,降低到可以接受的程度。
3.1.2 风险评估程序可根据项目的实际情况和选择的风险分析方法,在本标准第3.1.1条的基础上进行增减。
3.2 风险评估阶段和内容
3.2.1 医药工程项目风险评估可分为立项阶段、验收阶段、生产运行阶段。
3.2.2 立项阶段风险评估应根据建设项目可行性研究报告的内容确定,并应包括下列内容:
1 分析和预测系统的危险、有害因素及其程度;
2 提出消除、预防和降低危险、危害后果的对策措施;
3 评价采取措施后的系统是否能满足规定的安全要求。
3.2.3 验收阶段风险评估应在建设项目竣工验收前、试生产运行正常后进行。验收阶段风险评估应包括下列内容:
1 检查建设项目中安全设施是否已与主体工程同时设计、同时施工、同时投入生产和使用;评价建设项目及与之配套的安全设施是否符合国家有关安全生产的法律法规和技术标准。
2 通过对系统存在的危险和有害因素进行定性和定量的检查,从整体上评价建设项目的运行状况和安全管理是否正常、安全、可靠。
3 提出安全对策措施与建议。
4 评价系统是否达到正式投产所需的安全要求。
3.2.4 生产运行阶段在建设项目运行一定时间后,应依据国家法律法规或企业管理者认为有必要时进行风险评估。生产运行阶段风险评估应包括下列内容:
1 全面收集评价所需的信息资料,采用合适的安全评价方法进行危险识别、给出量化的安全状态参数值;
2 对于可能造成重大后果的事故隐患,采用合适的数学模型,进行事故模拟,预测极端情况下的影响范围,分析事故的最大损失,以及发生事故的概率;
3 对发现的隐患,根据量化的安全状态参数值、整改的优先度进行排序;
4 提出安全对策措施与建议。
.
4 风险分析方法
4.1 风险分析方法分类
4.1.1 风险分析可采用定性、半定量、定量以及几种分析相结合的方法。
4.1.2 常用的定性分析可选择下列方法:
1 安全检查表法;
2 类比法;
3 现场调查法;
4 头脑风暴法;
5 危险可操作性研究;
6 故障类型与影响分析法;
7 其他。
4.1.3 常用的半定量分析可选择下列方法:
1 风险矩阵法;
2 层次分析法;
3 影响图分析法;
4 作业条件危险性评价法(格雷厄姆-金尼法或LEC法);
5 故障树分析(FTA);
6 其他。
4.1.4 定量分析可采用模型模拟、试验研究或历史数据外推等方法。常用的定量分析可选择下列方法:
1 概率法;
2 指数法;
3 事故后果模拟分析法;
4 其他。
4.2 风险分析方法的选择
4.2.1 风险分析方法应根据下列因素确定:
1 医药工程项目的规模和复杂程度;
2 项目涉及的原料、产品的危险程度及作业环境;
3 合同或业主要求评估的具体目标和最终结果;
4 被评估系统技术资料、数据的完整程度;
5 评估所处阶段;
6 法律法规要求;
7 评估人员的知识、经验和习惯。
4.2.2 下列情况应采用定性分析:
1 作为初选,以决定此风险是否需要进行进一步的分析;
2 使用定性分析便可做出决策,不需投入更多的时间和精力;
3 没有足够的资料和资源进行定量分析或无法赋值。
4.2.3 风险评估宜根据医药工业的实际情况,采用下列一种或几种方法进行:
1 预先危险分析(PHA);
2 故障假设分析(What-If);
3 安全检查表分析(Safe Checklist);
4 故障假设/安全检查表分析(What-If/Safe Checklist);
5 危险与可操作性研究(HAZOP);
6 故障类型和影响分析(FMEA);
7 故障树分析(FTA);
8 作业条件危险性评价法(格雷厄姆-金尼法或LEC法);
9 危害分析关键控制点(HACCP),可按本标准附录C的规定进行分析;
10 事故后果模拟分析;
11 其他适用的方法。
4.2.4 医药工业风险评估方法应根据评估阶段,按本标准附录D和附录E进行选择。
.
5 风险评估
5.1 前期准备
5.1.1 风险评估进行前应熟悉评估的项目概况,分析工艺流程的安全可靠性,收集可靠的工艺参数,确认压力、温度、液位、流量、反应活性、腐蚀性等工艺条件和特点。
5.1.2 风险评估应确认危险化学品安全数据表(MSDS)及有关数据资料。
5.1.3 风险评估应了解项目的周边环境,收集当地的水文气象、工程地质资料,以及当地供水、供电、供气资料以及“三废”排放要求。
5.2 危险、有害因素辨识
5.2.1 风险评估应根据危险化学品安全数据表(MSDS)及有关数据资料,对工艺过程的原料、中间体、副产品、最终产品以及催化剂、溶剂、杂质、排放物等所有物料进行危险、有害因素辨识,并应符合下列要求:
1 应定性或定量确定危险化学品的危险特性和危险程度;
2 应确定危险化学品的过程存量和总量;
3 应确认危险化学品与危险化学品之间的相容性;
4 应确认物料与设备材料之间的相容性;
5 应确认危险化学品的使用、加工、储存、转移过程的技术要求以及存在的危险性;
6 应根据现行国家标准《危险化学品重大危险源辨识》GB 18218辨识危险化学品重大危险源。
5.2.2 生产过程的危险源辨识应根据总平面布置图、工艺流程图、设备布置图等相关图纸,危险化学品基础安全数据以及物料危险源分析的结果确定,并应符合下列要求:
1 应辨识生产工艺的危险性;
2 应辨识生产设施发生火灾、爆炸、泄漏等危险和危害的可能性及严重程度;
3 应辨识不同装置之间发生事故的相互影响;
4 应辨识各车间之间发生事故的相互影响;
5 应辨识项目与周边环境之间的相互影响;
6 应辨识当控制措施失效时,是否会发生人员受到伤害、设备遭受破坏等事故;
7 应辨识导致危险源发展成不期望事件或事故的原因;
8 应辨识温度、流速、压力、料位等工艺参数达到或超过极值的可能性。
5.2.3 可研阶段风险评估应根据总平面布置方案图、周边设施区域图、建设项目内在危险源分析的结果,以及搜集、调查和整理建设项目的外部情况,对建设项目的可行性进行分析,并应提出项目决策的建议。
5.3 风险评估单元及评估内容
5.3.1 风险评估单元可根据项目选址、总图布置、生产过程及设施、储存设施、辅助工程、生产管理等确定。
5.3.2 项目选址单元评估宜采取安全检查表法。评估应包括下列内容:
1 国家工业布局、城镇总体规划及土地利用总体规划要求;
2 自然危害因素对项目的影响;
3 周边环境对项目的影响;
4 项目对周边环境的影响。
5.3.3 总图布置单元评估宜采取安全检查表法。评估宜包括下列内容:
1 功能分区布置的合理性;
2 防火间距及安全、卫生防护距离满足国家相关标准的程度;
3 风向、日照等自然因素的影响。
5.3.4 选址及总图布置的安全检查表检查项可按本标准附录第B.0.1条进行编制,应按国家现行标准《化工企业总图运输设计规范》GB 50489、《工业企业总平面设计规范》GB 50187、《化工企业安全卫生设计规范》HG 20571和《生产过程安全卫生要求总则》GB/T 12801的有关规定执行。
5.3.5 生产过程及设施、仓储单元评估可根据医药工程项目的实际情况和评估阶段,按本标准第4.2节的规定选择一种或几种评估方法。安全检查表检查项可按本标准附录第B.0.2条~第B.0.4条进行编制。评估时应辨识下列因素:
1 危险源对全系统的影响,对其他单元的影响;
2 毗邻车间(装置)的相互影响;
3 单元评估时应辨识车间、装置的正常操作、减量操作、正常开车、正常停车、紧急停车、试车和其他特殊操作方式;
4 应对已采用的安全设施,特别是相互关联的一次响应、二次响应甚至多次响应的设施进行识别和评估。
5.3.6 辅助工程电气单元评估宜根据医药工业的实际情况及电气工程特点确定,宜采用安全检查表法,也可采用定量评价方法。安全检查表检查项可按本标准附录第B.0.5条进行编制。
5.3.7 生产管理单元评估宜采用安全检查表法。安全检查表检查项可按本标准附录第B.0.6条进行编制。
5.4 风险水平确定
5.4.1 事件发生的可能性和后果严重性应采用适当的方法确定,并应判断事件对评估对象的影响。风险水平应按图5.4.1确定,也可按下式计算:
式中:R——风险水平;
f——风险的计算函数;
P——风险发生的可能性;
S——风险后果的严重性。
图5.4.1 风险水平确定方法
5.4.2 数据充足时,风险发生的可能性及后果的严重性应根据相关数据采用概率法、指数法等定量方法确定,并应根据风险发生的可能性以及后果严重性,计算风险水平。
5.4.3 数据不足时,风险发生的可能性及后果的严重性宜采用定性或半定量方法确定。风险可能性属性的度量可按表5.4.3-1执行,风险后果属性的度量可按表5.4.3-2执行。
表5.4.3-1 风险可能性属性的度量
表5.4.3-2 风险后果属性的度量
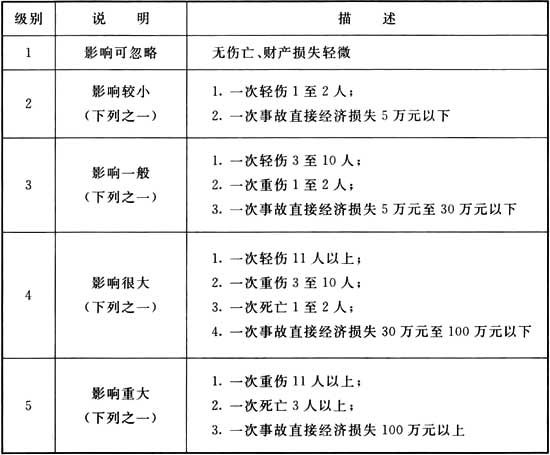
5.5 风险评估
5.5.2 确定风险等级应符合下列规定:
1 数据充足时,应将计算出的风险水平与风险准则进行比较,确定风险等级。风险准则应按采用的方法结合现场情况确定。当风险不可接受时,应采取更严格的安全措施。
2 数据不足时,应根据风险分析推断出的风险发生的可能性以及后果严重性,采用风险矩阵法确定风险等级。风险矩阵应符合表5.5.2的要求。
表5.5.2 风险矩阵——风险等级
5.5.3 判定风险结果应符合下列规定:
1 低、中、高、极高四级风险宜对应可接受、不可接受两个层次。评估方应根据自身实际情况判定风险是否可接受。
2 当风险可接受时,应保持已有的安全措施;当风险不可接受时,应采取更严格的安全措施。
附录A 风险评估程序
图A 风险评估程序
附录B 安全检查表
表B.0.1 选址、总平面布置安全检查表
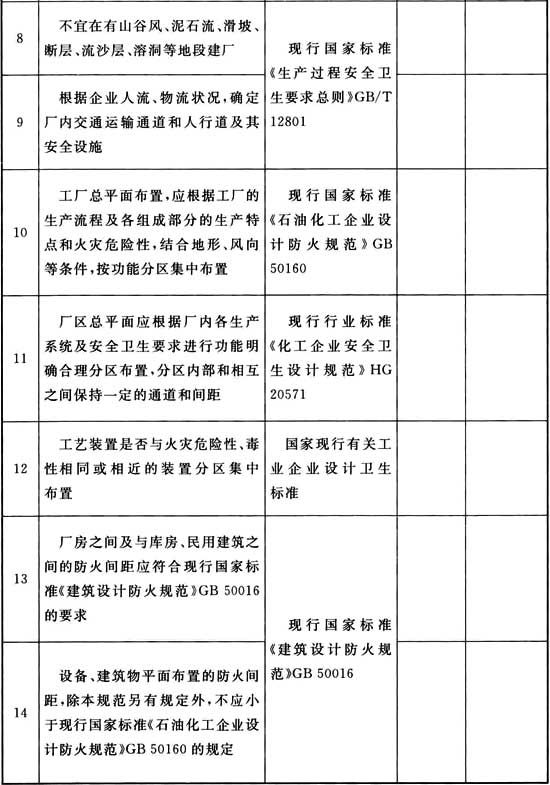
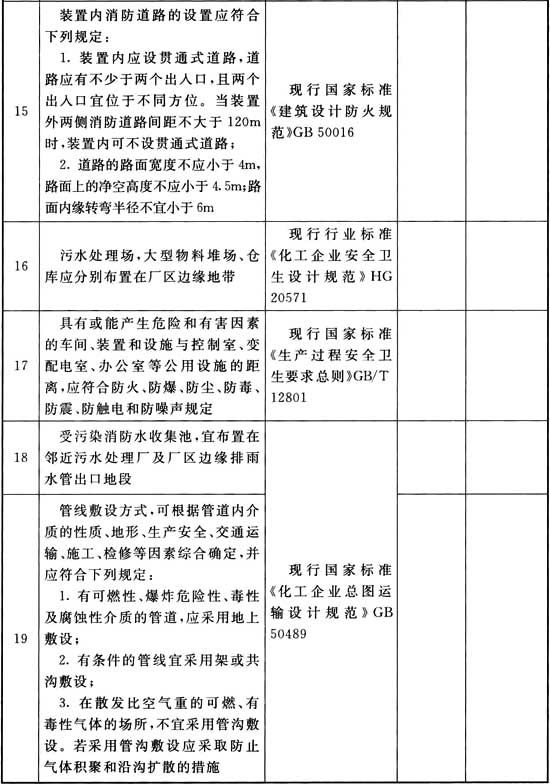
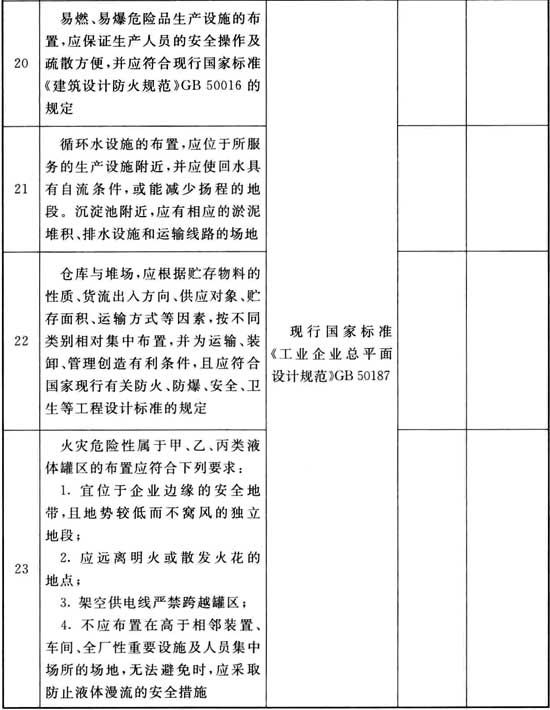
注:一般医药企业要求的防火间距应符合现行国家标准《建筑设计防火规范》GB 50016的要求;具有爆炸危险性的建设项目,其防火间距应符合现行国家标准《石油化工企业设计防火规范》GB 50160的要求。
B.0.2 工艺安全检查表应按表B.0.2编制。
表B.0.2 工艺安全检查表
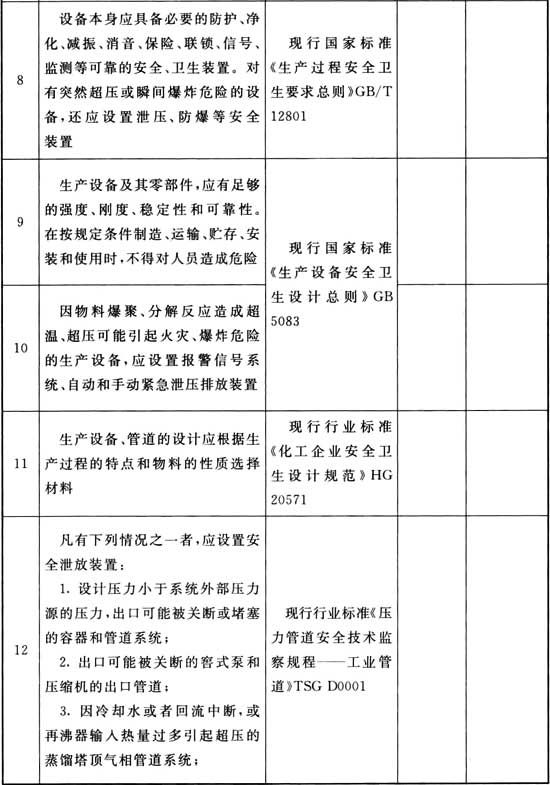
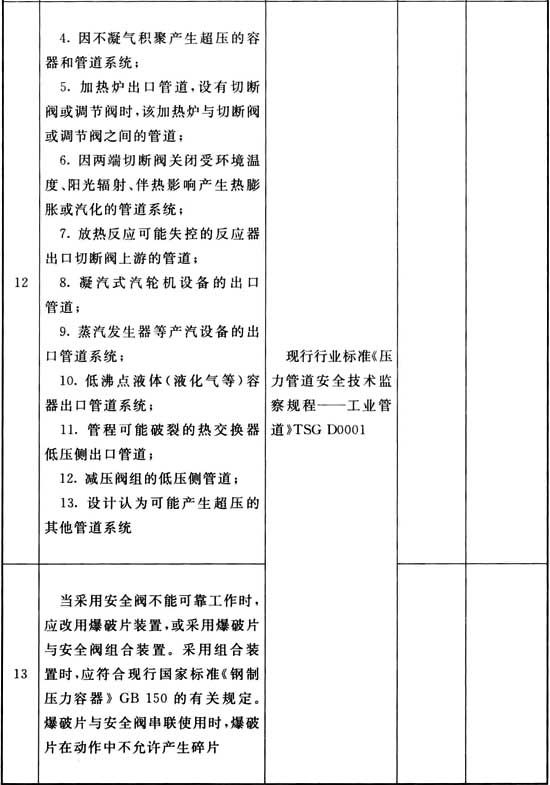
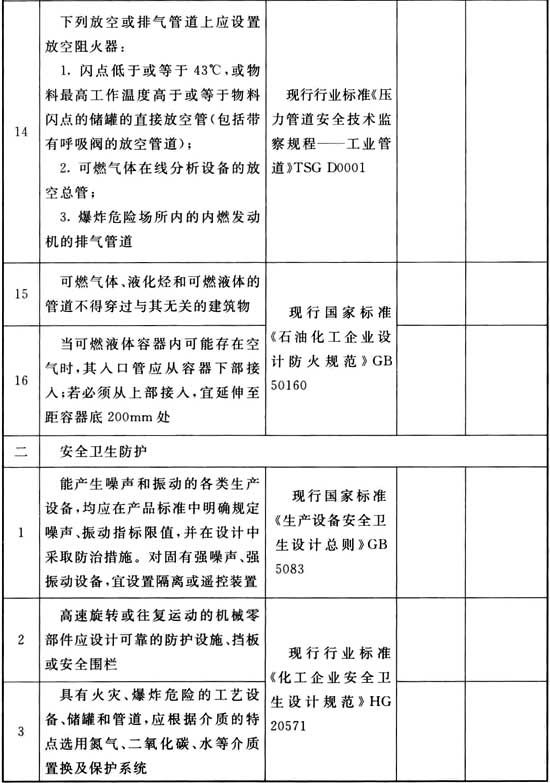
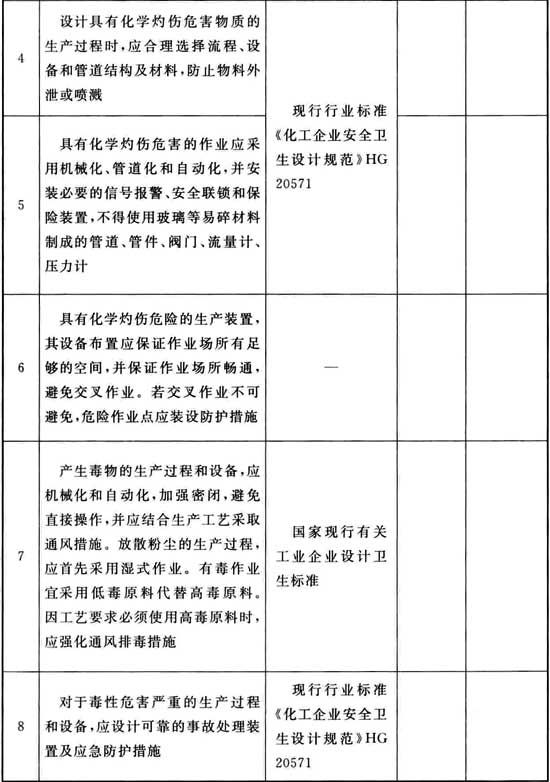
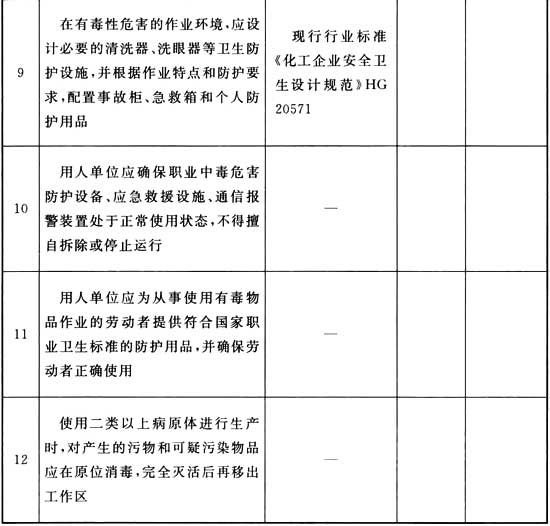
B.0.3 建筑安全检查表应按表B.0.3编制。
表B.0.3 建筑安全检查表
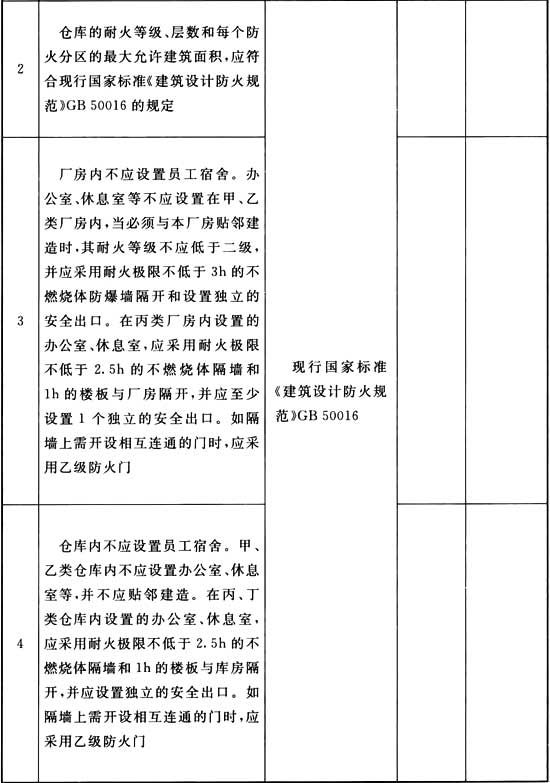

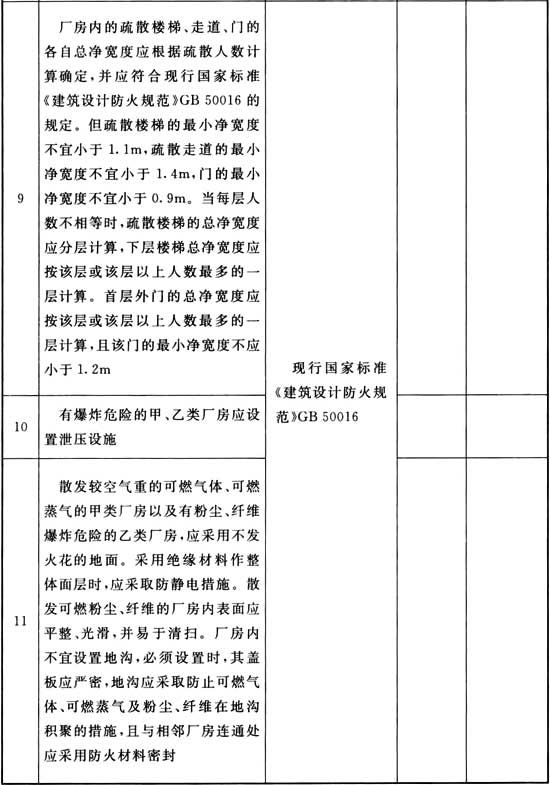
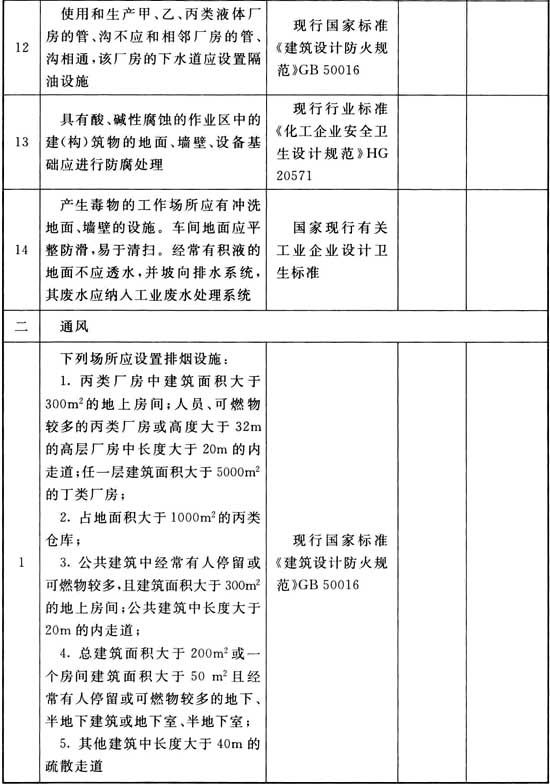
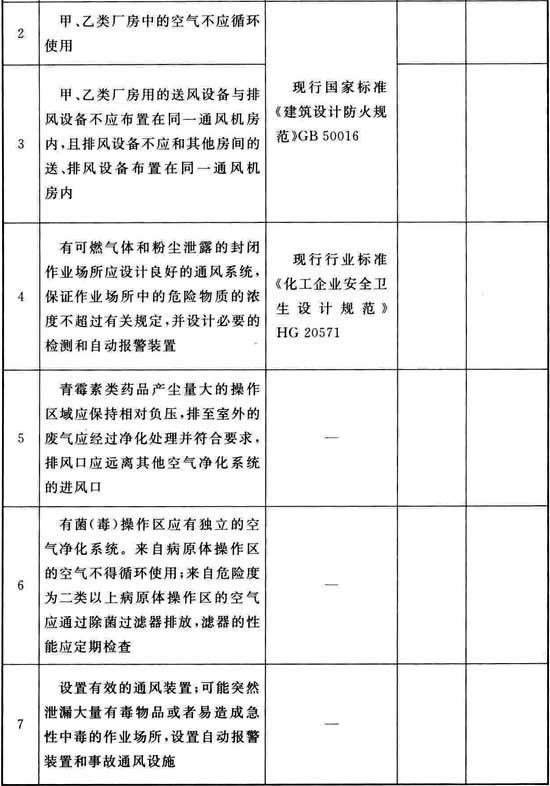
B.0.4 储存设施安全检查表应按表B.0.4编制。
表B.0.4 储存设施安全检查表
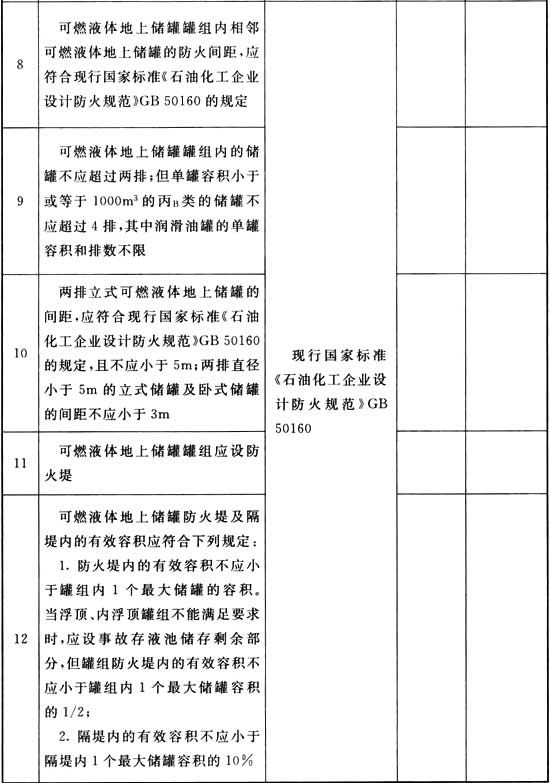
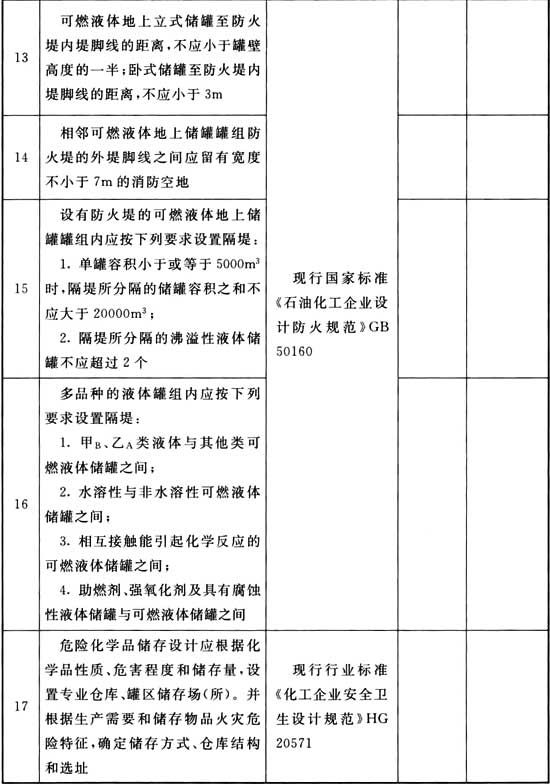
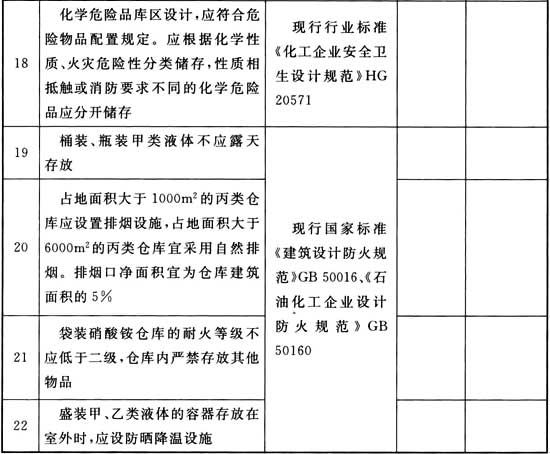
B.0.5 电气部分安全检查表应按表B.0.5编制。
表B.0.5 电气部分安全检查表
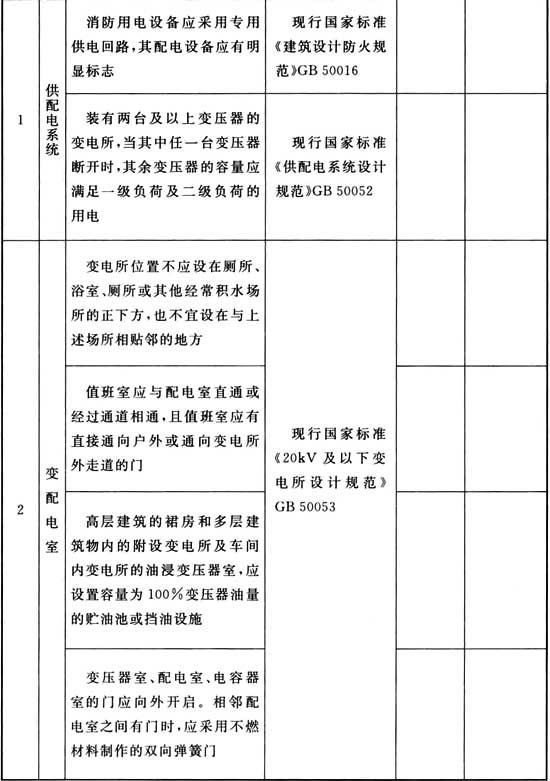
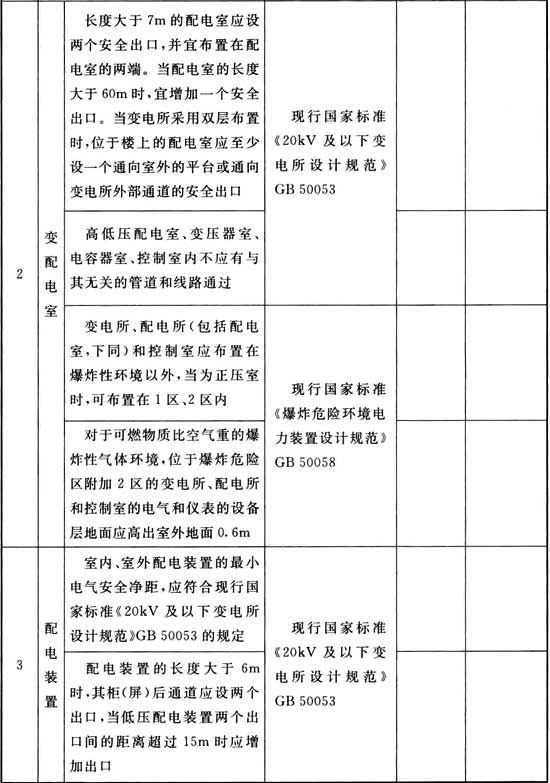
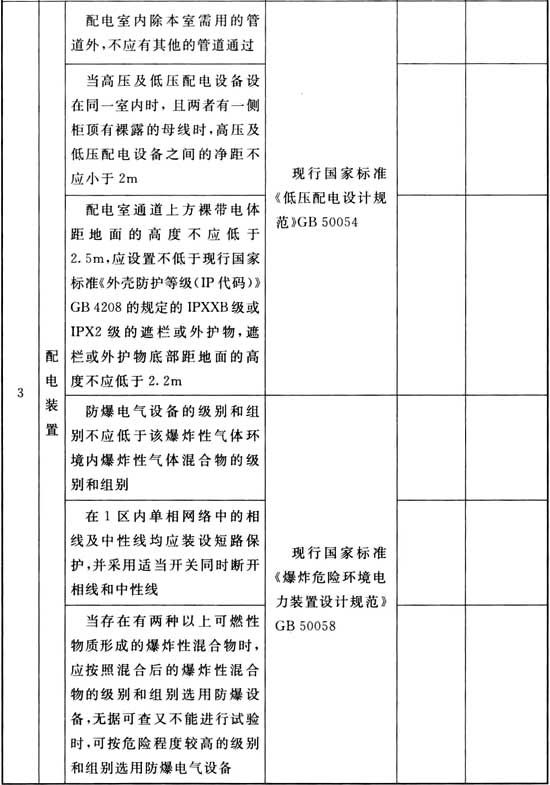

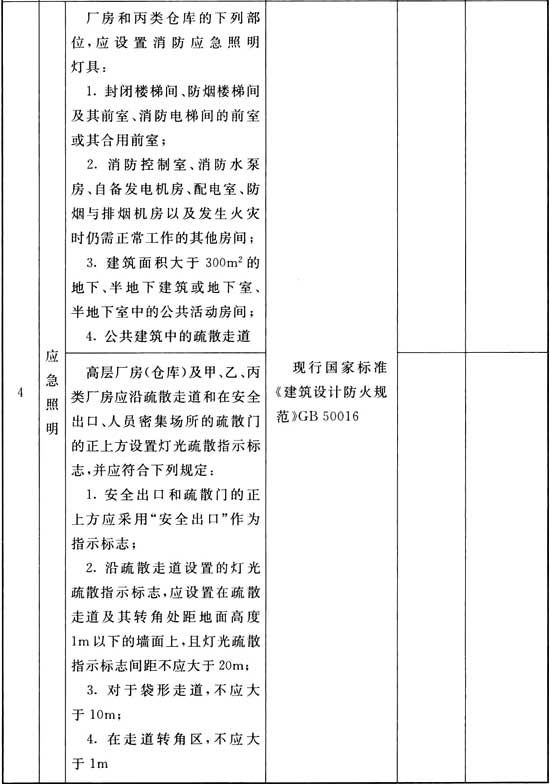
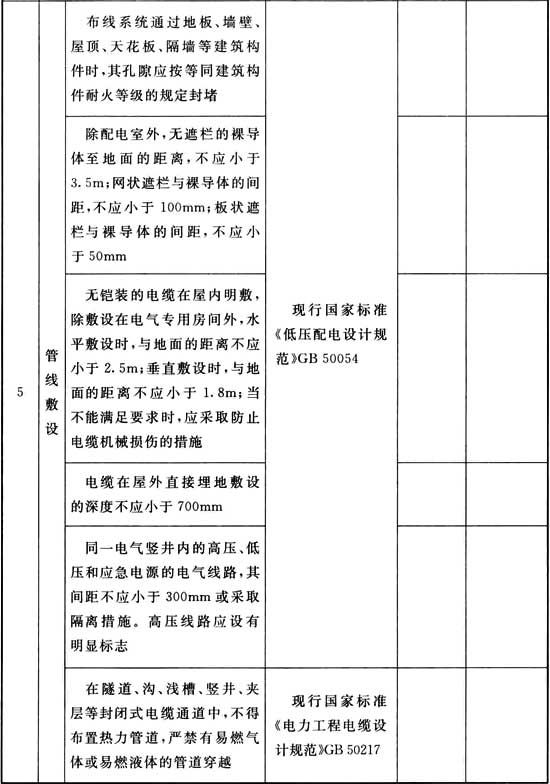


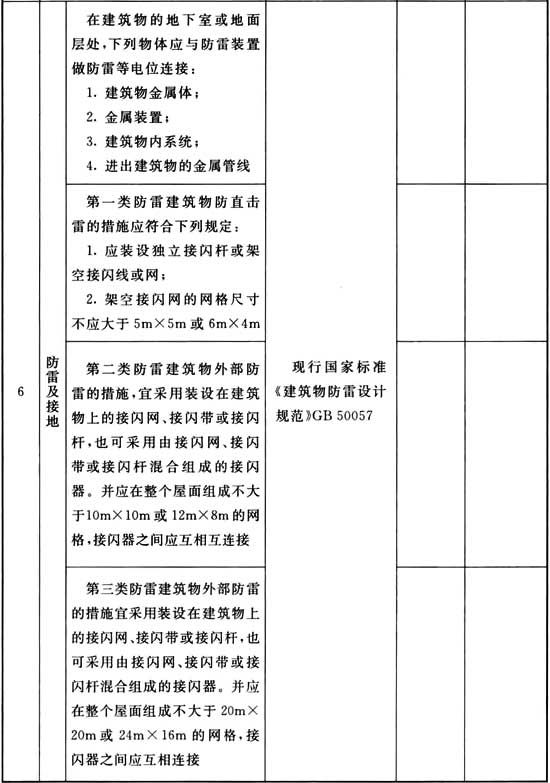
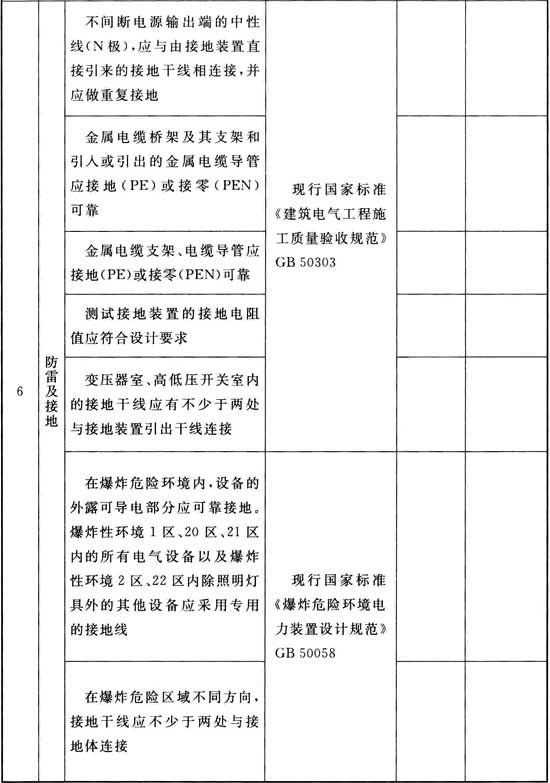
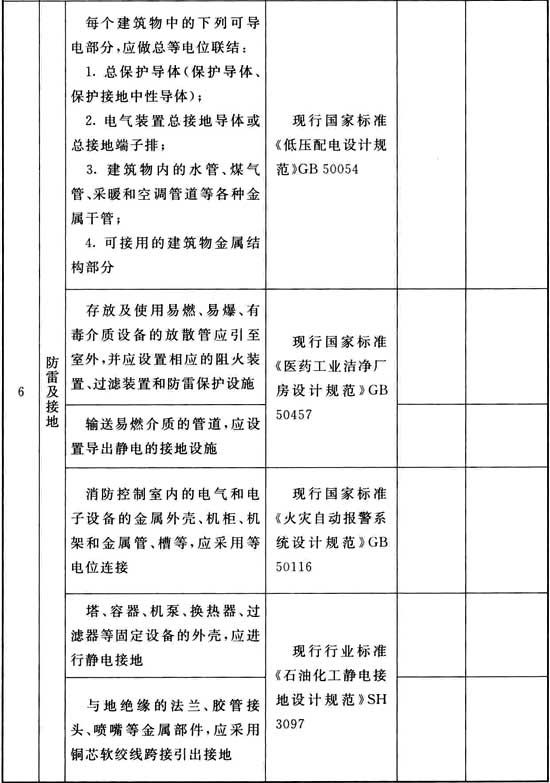



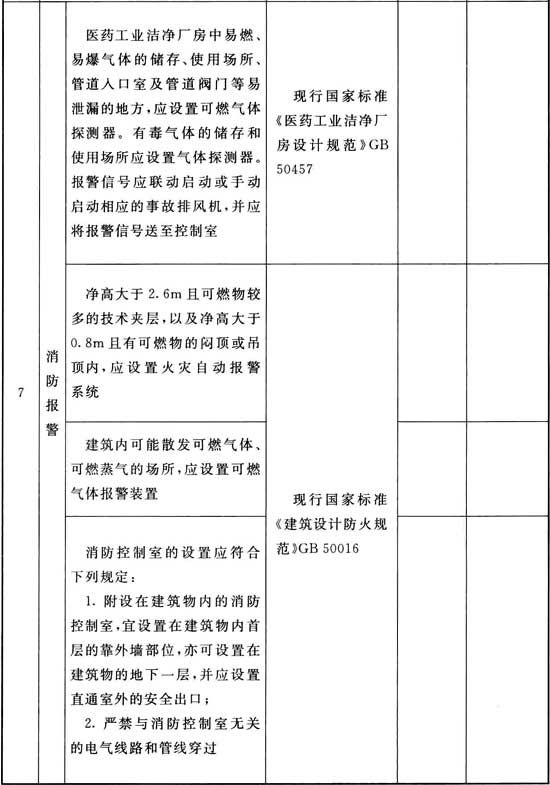


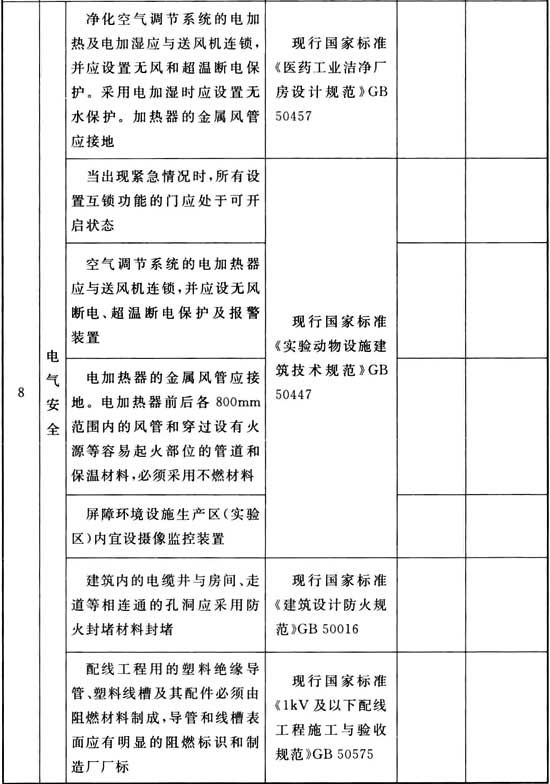
B.0.6 生产(安全)管理单元安全检查表应按表B.0.6编制。
表B.0.6 生产(安全)管理单元安全检查表

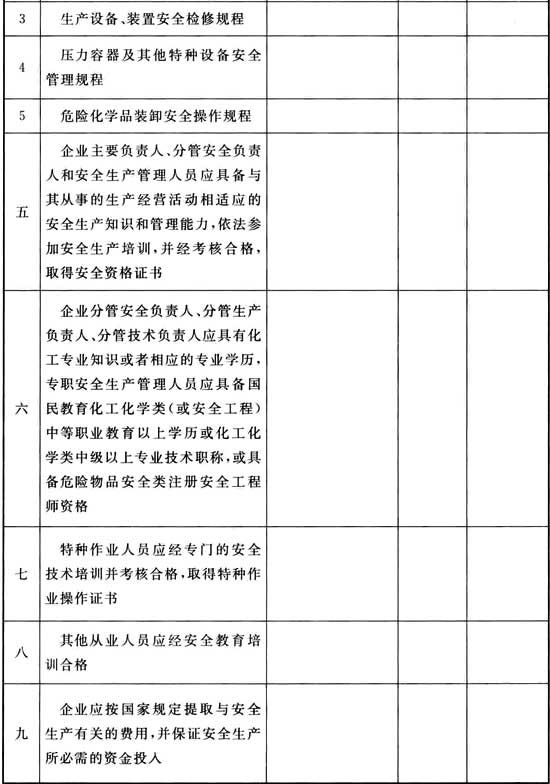
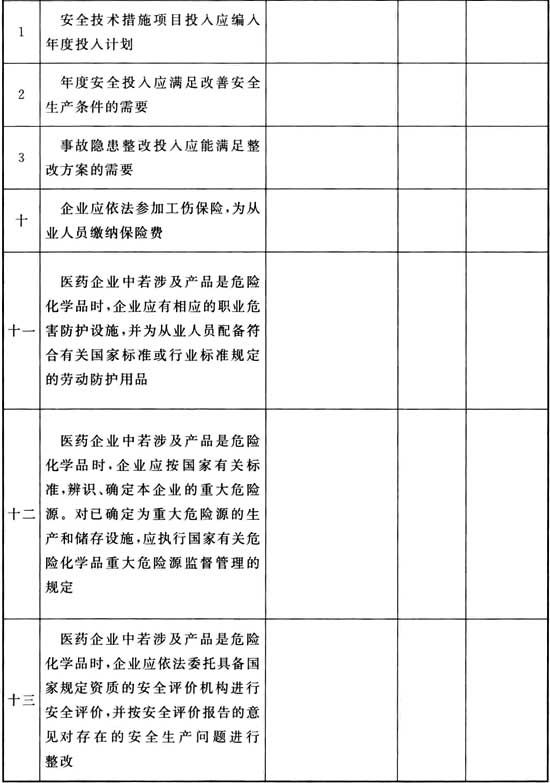
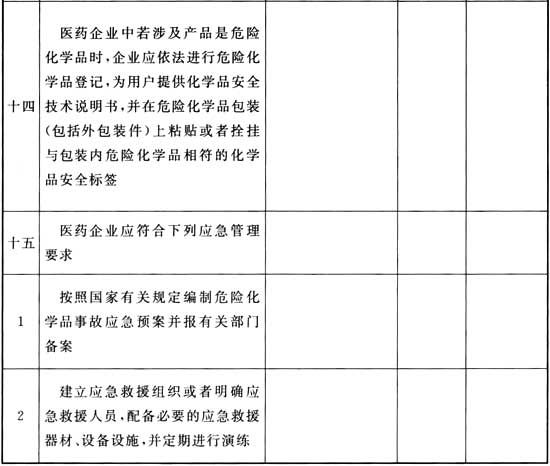
注:1 安全检查表的内容根据原料药企业的情况编写,制剂类或其他医药企业可根据其具体情况做相应的增减;
2 检查结果以“符合”或“不符合”表示。
附录C 危害分析关键控制点
C.0.1 危害分析关键控制点应包括下列内容:
1 对过程的每一步进行危险分析并辨识预防措施;
2 确定关键控制点;
3 建立目标水平和关键限值关键限度;
4 建立监测关键控制点的监控体系;
5 建立当监测显示关键控制点并不在控制状态时应该采取的纠正措施;
6 建立证实危害分析关键控制点体系在有效运转的系统;
7 建立一个保持记录的系统。
C.0.2 危害分析关键控制点的实施应包括下列步骤:
1 组建危害分析关键控制点小组。危害分析关键控制点小组成员应具有关于药品及其生产工艺的专业知识和经验,现场的小组成员也不具备某方面的专业经验时,应咨询其他专家的意见。应明确规定危害分析关键控制点计划的适用范围,要具体到整个过程的每个阶段,并确认出现危害的种类。
2 对产品及生产工艺的说明。应对产品及生产过程进行完整的描述和说明,包括组成、物理/化学性质、结构、pH值、温度、清洁方法、灭菌方法、烘干、过筛、混合、包装以及贮藏条件、销售及运输方法等相关质量信息。对于热不稳定的产品更应说明产品的销售及运输方法。
3 确定产品的预期用途。产品预期用途的确定应基于最终使用者或消费者所期望的用途。
4 绘制流程图。流程图应覆盖工艺过程的所有操作步骤及决策。当绘制某一特定的操作时,其前后步骤均应有所联系。
5 现场确认流程图。流程图中列出的每一个步骤必须在生产现场进行确认。危害分析关键控制点小组应通过现场观察操作,确认绘制的流程图与实际生产是否一致。必要时可对流程图进行修改,且应进行记录。
6 应列出和每一生产步骤相关的潜在危害,进行危害分析,建立各种可以控制危害的措施。进行危害分析时,安全方面与质量方面应有所区分。危害分析关键控制点小组应列出整个生产、检验销售直至使用过程中所有可能出现的危害。然后应进行危害分析以确认危害分析关键控制点计划可将危害消除或将其降低到可以接受的程度。
7 确定关键控制点(CCP)。确认某一步骤存在危害,为确保安全应对此步骤进行监控却没有相应的监控措施时,应对该步骤的产品或工艺过程进行调整,或在其前后的步骤中建立相应的监控措施。
8 对每个关键控制点建立关键限值。应规定每一个关键控制点的关键限值并经过验证。常用的参数应包括对温度、时间、湿度、pH值以及外观参数的测量,关键限值的规定应建立在科学的基础上。
9 对每个关键控制点建立监测系统。监测应按预定的计划进行测量或观察,并应准确记录。监测程序应能够及时检测出关键控制点的失控之处,并及时准确地获得该信息以对其进行调整。当监控结果显示一个关键控制点有失控倾向时,应在偏差发生前对生产过程进行调整。所有有关关键控制点监测的记录及文件均应由实施监测的人员和公司的核查负责人签名,并注明日期。
10 建立纠正措施。应事先建立针对每一个关键控制点的纠正措施,并将其列入危害分析关键控制点计划中,危害分析关键控制点计划应至少详细说明偏差发生时如何纠正、由谁来负责实施纠正措施,且纠正措施的实施应详尽记录并保存。措施应确保关键控制点处于受控状态之下。纠正措施应至少包括下列内容:
1)确定和纠正引起偏差的原因;
2)确定如何处理在偏离期间生产的产品;
3)记录实施的纠正措施。
11 建立校验程序。应建立校验程序(verification proce-dures),校验的频率应确保危害分析关键控制点体系的正常功能。校验应包括下列内容:
1)危害分析关键控制点体系及其记录的审查;
2)偏差以及产品处置的审查;
3)确认关键控制点处于受控状态之下。
12 建立文件并保存记录。要求建立文件的活动应包括下列内容:
1)危害分析;
2)关键控制点的确定;
3)危害分析关键控制点计划;
4)关键限值确定。
13 要求保存记录的活动应包括下列内容:
1)关键控制点监测活动;
2)工艺步骤;
3)相关危害;
4)关键限值;
5)校验程序和时间表;
6)偏离;
7)相关的纠正措施;
8)危害分析关键控制点体系的调整。
C.0.3 危害分析关键控制点小组成员应具有下列能力:
1 能够进行危害分析;
2 能够确认潜在危害;
3 能够确认应控制的危害;
4 能够提出关键控制和关键限值;
5 能够建立监控和核查程序;
6 能够提出在出现偏差时的纠正措施;
7 能够审核危害分析关键控制点方案。
C.0.4 危害分析关键控制点可用于对与物理、化学和生物危险因素(包括微生物污染)有关风险的辨识及管理。
附录D 医药工业常用风险评估方法对照
表D 医药工业常用风险评估方法对照
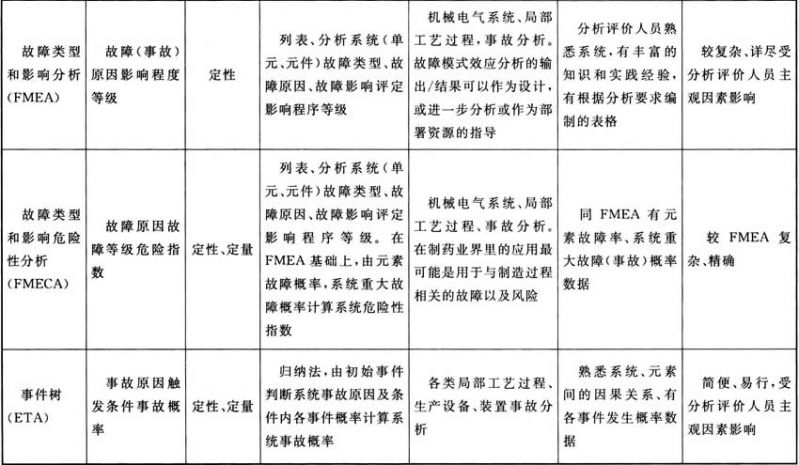
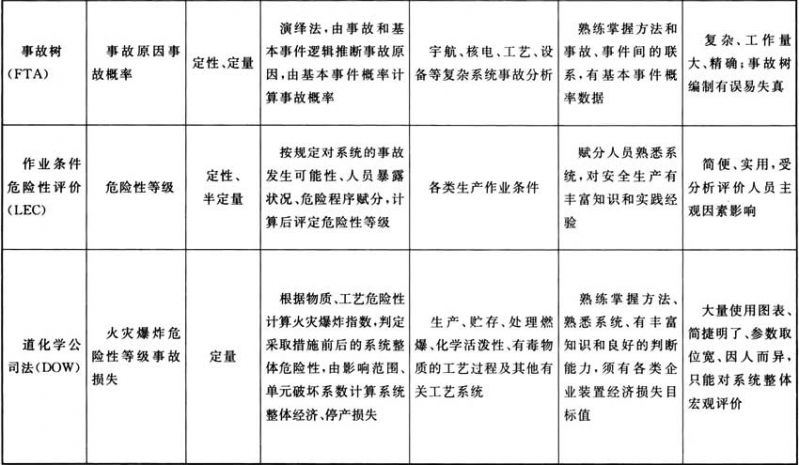
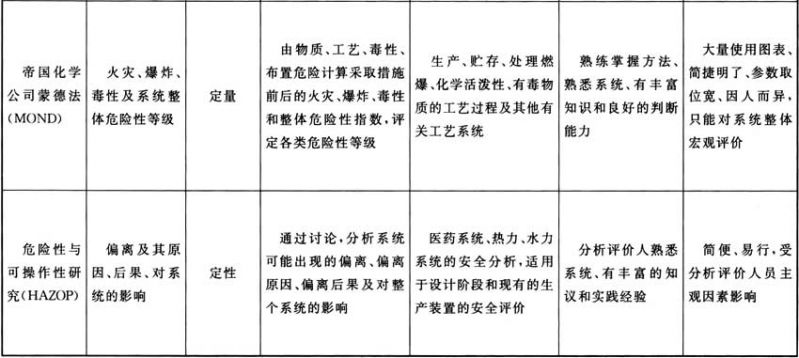
附录E 医药工业不同阶段可采用的风险评估方法
表E 医药工业不同阶段可采用的风险评估方法
2 危险指数法(RR)包括道化学火灾、爆炸指数法(DOW方法)、ICI蒙德法等。
本标准用词说明
1 为便于在执行本标准条文时区别对待,对要求严格程度不同的用词说明如下:
1)表示很严格,非这样做不可的:
正面词采用“必须”,反面词采用“严禁”;
2)表示严格,在正常情况下均应这样做的:
正面词采用“应”,反面词采用“不应”或“不得”;
3)表示允许稍有选择,在条件许可时首先应这样做的:
正面词采用“宜”,反面词采用“不宜”;
4)表示有选择,在一定条件下可以这样做的,采用“可”。
2 条文中指明应按其他有关标准执行的写法为:“应符合……的规定”或“应按……执行”。
引用标准名录
《建筑设计防火规范》GB 50016
《建筑照明设计标准》GB 50034
《供配电系统设计规范》GB 50052
《20kV及以下变电所设计规范》GB 50053
《低压配电设计规范》GB 50054
《建筑物防雷设计规范》GB 50057
《爆炸危险环境电力装置设计规范》GB 50058
《火灾自动报警系统设计规范》GB 50116
《石油化工企业设计防火规范》GB 50160
《火灾自动报警系统施工及验收规范》GB 50166
《电气装置安装工程接地装置施工及验收规范》GB 50169
《工业企业总平面设计规范》GB 50187
《电力工程电缆设计规范》GB 50217
《建筑电气工程施工质量验收规范》GB 50303
《入侵报警系统工程设计规范》GB 50394
《视频安防监控系统工程设计规范》GB 50395
《实验动物设施建筑技术规范》GB 50447
《医药工业洁净厂房设计规范》GB 50457
《化工企业总图运输设计规范》GB 50489
《工业企业电气设备抗震设计规范》GB 50556
《1kV及以下配线工程施工与验收规范》GB 50575
《钢制压力容器》GB 150
《外壳防护等级(IP代码)》GB 4208
《生产设备安全卫生设计总则》GB 5083
《生产过程安全卫生要求总则》GB/T 12801
《危险化学品重大危险源辨识》GB 18218
《工作场所有害因素职业接触限值》GBZ 2
《化工企业安全卫生设计规范》HG 20571
《石油化工静电接地设计规范》SH 3097
《压力管道安全技术监察规程——工业管道》TSG D0001