标准规范下载简介
在线阅读
中华人民共和国国家标准
建筑采暖用钢制散热器配件通用技术条件
General technical specification for steel heating radiator accessories
GB/T 32835-2016
发布日期:2016年8月29日 实施日期:2017年7月1日
中华人民共和国国家质量监督检验检疫总局
中国国家标准化管理委员会 发布
前言
本标准由中华人民共和国住房和城乡建设部提出。
本标准由全国暖通空调及净化设备标准化技术委员会(SAC/TC 143)归口。
本标准负责起草单位:天津市建筑采暖散热器行业协会、中国建筑金属结构协会采暖散热器委员会。
本标准参加起草单位:辽宁省建筑金属结构协会、沈阳市吉水暖气厂、国家散热器检测中心、辽宁省水暖器材产品质量监督检验中心、天津市建设工程技术研究所、天津市产品质量监督检测技术研究院、天津市供热办、天津市东丽区宝兴机械有限公司、天津市然发钢管有限公司、天津市金立钢管有限公司、廊坊爵蒙暖通设备有限公司、廊坊舒适塑钢制品有限公司、芦台经济开发区金鑫董金属制品厂、天津金力通金属制品有限公司、天津市津暖散热器配件厂、唐山大通金属制品有限公司、山东邦泰散热器有限公司、哈尔滨帽儿山暖气片有限责任公司、佛山市太阳花散热器有限公司。
本标准主要起草人:赵卫平、吴辉敏、宋为民、陈明、王毅、齐嘉卉、杨金元、侯柏岩、支家强、许仕君、周志刚、王延升、李文晋、刘茂柏、孟凯、彭石磊、闫涛、高云飞、王久长、于克跃、夏世鹏、梁斌、罗卫东、王贺。
1 范围
本标准规定了建筑采暖用钢制散热器配件的术语和定义、分类与标记、结构、要求、试验方法、检验规则以及合格证、包装和贮运。
本标准适用于符合GB/T 29039规定的钢制采暖散热器的片头、钢管、螺纹管口、丝堵、放气丝堵主要配件。
2 规范性引用文件
下列文件对于本文件的应用是必不可少的。凡是注日期的引用文件,仅注日期的版本适用于本文件。凡是不注日期的引用文件,其最新版本(包括所有的修改单)适用于本文件。
GB/T 223.60 钢铁及合金化学分析方法 高氯酸脱水重量法测定硅含量
GB/T 223.62 钢铁及合金化学分析方法 乙酸丁酯萃取光度法测定磷量
GB/T 223.63 钢铁及合金化学分析方法 高碘酸钠(钾)光度法测定锰量
GB/T 223.67 钢铁及合金 硫含量的测定 次甲基蓝分光光度法
GB/T 223.71 钢铁及合金化学分析方法 管式炉内燃烧后重量法测定碳含量
GB/T 241 金属管 液压试验方法
GB/T 699 优质碳素结构钢
GB/T 700 碳素结构钢
GB/T 985.1 气焊、焊条电弧焊、气体保护焊和高能束焊的推荐坡口
GB 2102 钢管的验收、包装、标志和质量证明书
GB/T 2828.1 计数抽样检验程序 第1部分:按接收质量限(AQL)检索的逐批检验抽样计划
GB/T 6461-2002 金属基体上金属和其他无机覆盖层 经腐蚀试验后的试样和试件的评级
GB/T 7307 55°非密封管螺纹
GB/T 10125 人造气氛腐蚀试样 盐雾试验
GB/T 12467.3 金属材料熔焊质量要求 第3部分:一般质量要求
GB/T 19866 焊接工艺规程及评定的一般原则
GB/T 29039 钢制采暖散热器
QB/T 3834 轻工产品金属镀层和化学处理层的厚度测试方法 磁性法
3 术语和定义
下列术语和定义适用于本文件。
3.1
片头 terminal part
冷轧钢板经冲压成型,与钢管对接焊组成钢制采暖散热器的部件。由两块材料加工成型的片头为合体片头,由单块材料加工成型的片头为整体片头。
3.2
螺纹管口 screwed connector
焊接在散热器上与供暖系统连接的螺纹部件。
3.3
丝堵 pipe plug
封堵钢制采暖散热器的螺纹配件。
3.4
放气丝堵 radiator vent cock
安装在散热器上,用于手动排除空气的装置。
4 分类与标记
4.1 分类
钢制采暖散热器配件包括片头、钢管、螺纹管口、丝堵、放气丝堵,分别用PT、G、LG、S、FS表示。
4.2 标记
4.2.1 片头
示例:
立管为圆管,管径为Ф40mm,两柱,宽度为100mm,高度为90mm的片头,其标记为:PT-Y-40/2-100×90。
4.2.2 钢管
示例:
圆管,材质牌号为Q195,管径为Ф40mm,壁厚为1.5mm的焊接钢管,其标记为:YG-H-Q195-40-1.5。
4.2.3 螺纹管口、丝堵、放气丝堵
示例:
钢质、公称直径为G3/4的螺纹管口,其标记为:LG-G-G3/4。
5 结构
片头、钢管、螺纹管口、丝堵、放气丝堵示意图分别见图1~图8。
说明:

B——宽度;
H——高度;
H1——片头水口中心至片头和钢管对焊端面部位的高度;
L——厚度;
L1——椭圆管顶部至合体片头对焊部位厚度。
图1 两柱(椭圆管)合体片头示意图
说明:

B——宽度;
H——高度;
H1——片头水口中心至片头和钢管对焊端面部位的高度;
L——厚度;
L1——片头与钢管对焊端面部位的厚度。
图2 两柱(椭圆管)整体片头示意图
说明:

B——宽度;
H——高度;
H1——片头水口中心至片头和钢管对焊端面部位的高度;
L——厚度;
L1——片头与钢管对焊端面部位的厚度。
图3 三柱(圆管)整体片头示意图
说明:

B——宽度;
H——高度;
H1——片头水口中心至片头和钢管对焊端面部位的高度;
L——厚度;
L1——圆管顶部至合体片头对焊部位厚度。
图4 三柱(圆管)合体片头示意图
L——长度。
图5 钢管示意图
图6 螺纹管口示意图
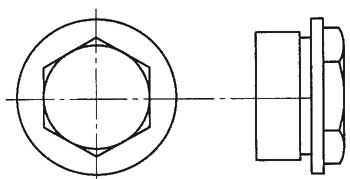
图7 丝堵示意图
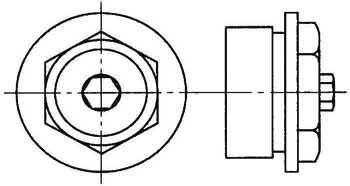
图8 放气丝堵示意图
6 要求
6.1 片头
6.1.1 片头钢板牌号为ST12冷轧钢板的化学成分应符合表1的规定或等同采用该化学成分的其他材质。片头壁厚冲压后最薄部位不应小于1.5mm。
表1 冷轧钢板化学成分
C | Mn | Si | P | S |
≤0.10 | 0.20~0.45 | 痕量 | ≤0.045 | ≤0.045 |
6.1.2 片头管口端面椭圆尺寸为25mm×50mm时,椭圆度应为R39.2×R7;椭圆尺寸为30mm×60mm时,椭圆度应为R44×R7。
6.1.3 片头应平整,光滑,不应有裂纹、拉痕、扭曲、凹陷等缺陷。
6.1.4 焊接质量应符合如下要求:
a) 片头的焊接质量应符合GB/T 985.1、GB/T 12476.3和GB/T 19866的规定。
b) 片头焊接应牢固,焊接部位应平整光滑,不应有裂纹、气孔及未焊透和烧穿等缺陷。
c) 焊接后片头应平整,外观光滑,不应有明显变形。
6.1.5 片头外形尺寸与极限偏差应符合表2的规定,管口孔直径、宽度尺寸与极限偏差应符合表3的规定。
6.1.6 片头形位公差应符合表4的规定。
表2 片头外形尺寸与极限偏差 单位为毫米
高度 | 厚度 | ||||
H | H1 | L | L1 | ||
基本尺寸 | 极限偏差 | 极限偏差 | 基本尺寸 | 极限偏差 | 极限偏差 |
75~90 | ±0.25 | ±0.30 | 45~60 | ±0.20 | ±0.20 |
91~105 | ±0.30 | ≥70 | ±0.30 |
表3 管口孔直径、宽度尺寸与极限偏差 单位为毫米
管口孔直径(Ф) | 宽度(B) | ||
基本尺寸 | 极限偏差 | 基本尺寸 | 极限偏差 |
38~52 | ±0.20 | 80~145 | ±0.30 |
表4 片头形位公差 单位为毫米
项目 | 平行度(A) | 垂直度(B⊥A) |
形位公差 | ≤0.20 | ≤0.30 |
6.2 钢管
6.2.1 钢管厚壁材质应符合GB/T 699或GB/T 700的规定,且壁厚不应小于1.8mm;薄壁材质应符合GB/T 699中镇静钢的要求,且壁厚不应小于1.5mm。
6.2.2 钢管应光滑,不应有折叠、裂缝、气孔、分层、搭焊、麻点、氧化黑皮等缺陷。
6.2.3 钢管焊接应牢固,外焊缝毛刺应修磨平整。
6.2.4 椭圆管尺寸为25mm×50mm时,椭圆度应为R39.2×R7;尺寸为30mm×60mm时,椭圆度应为R44×R7。
6.2.5 圆管和椭圆管的工作压力应为1.5MPa。
6.2.6 钢管弯曲度应小于1mm/m。钢管的扭转值不应大于0.3mm/m。
6.2.7 钢管的不圆度不应大于直径允许偏差。
6.2.8 圆管的直径、壁厚及允许偏差应符合表5的规定;椭圆管、方管和D型管的外径、壁厚及允许偏差应符合表6的规定。
5 圆管的直径、壁厚及允许偏差 单位为毫米
表6 椭圆管、方管和D型管的外径、壁厚及允许偏差 单位为毫米
6.3 螺纹管口、丝堵、放气丝堵
6.3.1 螺纹管口、丝堵、放气丝堵材质应符合GB/T 699中Q235B的规定。螺纹不应有裂纹、丝扣应完整。
6.3.2 螺纹管口的螺纹不应少于5扣,丝堵的螺纹不应少于3.5扣。螺纹管口、丝堵的壁厚不应小于5mm。
6.3.3 螺纹管口、丝堵、放气丝堵的公称直径为G1/2、G1/4、G1、

6.3.4 丝堵镀层厚度应为8μm~10μm。
6.3.5 金属零件应具有耐腐蚀性,经盐雾试验后应符合GB/T 6461-2002中9级的规定。
6.3.6 螺纹管口轴线与螺纹外端面垂直度不应大于0.3mm。
6.3.7 螺纹管口同轴度不应大于0.5mm。
6.3.8 放气丝堵在旋开使用时应放气顺畅,旋紧时不应渗漏。
7 试验方法
7.1 片头
7.1.1 片头钢板的化学成分应按GB/T 223.60、GB/T 223.62、GB/T 223.63、GB/T 223.67、GB/T 223.71的规定进行检测。片头壁厚应用精度为0.001mm的外径千分尺检测。
7.1.2 片头管口端面椭圆尺寸应用精度为0.02mm的游标卡尺测量,椭圆度应用R规检测。
7.1.3 在自然光线下目测检验外观质量。
7.1.4 在自然光线下目测检验焊接质量。
7.1.5 片头外形尺寸、管口孔直径和宽度尺寸与极限偏差应采用精度为0.02mm的通用量具检测。
7.1.6 片头形位公差应用0.01级塞尺、0级宽座直角尺和精度为0.01mm高度尺及不低于三级的平台配合检验。
7.2 钢管
7.2.1 钢管材质应按GB/T 700的规定进行检测,壁厚应用精度为0.001mm的壁厚千分尺测量。
7.2.2 在自然光线下目测检验外观质量。
7.2.3 在自然光线下目测检验焊接质量。
7.2.4 椭圆管的椭圆尺寸应用精度为0.02mm的游标卡尺测量,椭圆度应用R规检测。
7.2.5 钢管的压力试验应按GB/T 241的规定进行检测,压力计精度不低于1.5级,量程为2.5MPa。
7.2.6 钢管弯曲度及扭转值应用0.01级塞尺和不低于三级的平台配合检验。
7.2.7 钢管的不圆度应用精度为0.02mm的游标卡尺测量。
7.2.8 圆管的直径、壁厚及允许偏差应用精度为0.02mm的游标卡尺测量。椭圆管、方管和D型管的外径、壁厚及允许偏差应用精度为0.02mm的游标卡尺测量。
7.3 螺纹管口、丝堵、放气丝堵
7.3.1 材质应按GB/T 700的规定进行检测,在自然光线下目测检验外观质量。
7.3.2 在自然光线下目测检验螺纹扣数,螺纹管口、丝堵、放气丝堵的壁厚应用精度为0.01mm的管式外径用千分尺检验。
7.3.3 螺纹制作精度应用B级螺纹环规和螺纹塞规进行检测。
7.3.4 丝堵金属镀膜的厚度应按QB/T 3834的规定进行试验。
7.3.5 金属表面的耐腐蚀性检验应按GB/T 10125中的中性盐雾(NSS)相关规定进行盐雾试验,样板试验时间为72h。
7.3.6 螺纹管口轴线与螺纹外端面垂直度应用螺纹环规和塞尺进行检验。
7.3.7 螺纹管口同轴度应用精度为0.02mm的游标卡尺测量。
7.3.8 放气丝堵的试验压力应为1.5MPa,将放气丝堵整体浸入试验水槽中,稳压时间为1min,在稳压时间内放气丝堵不渗漏或不冒气泡为合格。压力计精度不应低于1.5级,量程为2.0MPa。
8 检验规则
8.1 检验分类
片头、钢管、螺纹管口、丝堵、放气丝堵检验分为出厂检验和型式检验。
8.2 出厂检验
8.2.1 片头、钢管、螺纹管口、丝堵、放气丝堵应经制造厂的质量检验部门检验合格后,方可出厂。
8.2.2 抽样方法及判定规则如下:
a) 片头、钢管、螺纹管口、丝堵、放气丝堵应按批进行检验。每批应由同一规格、同一品种的产品组成,每批钢管的数量不应超过如下规定:圆管1000支;异型管1000支。每批片头、螺纹管口、丝堵、放气丝堵的数量不应超过2000个。
b) 片头、螺纹管口、丝堵、放气丝堵应从批量中抽3‰进行检验,钢管应从批量中抽2‰进行检验。
8.2.3 片头出厂检验应按表7规定的项目进行。
表7 片头检验项目表
8.2.4 钢管出厂检验应按表8规定的项目进行。
表8 钢管检验项目表
8.2.5 螺纹管口、丝堵、放气丝堵出厂检验应按表9规定的项目进行。
表9 螺纹管口、丝堵、放气丝堵检验项目表
8.3 型式检验
8.3.1 有下列情况之一者,应进行型式检验:
a) 新产品或转产生产试制产品时;
b) 产品在设计、工艺或使用的材料有重大改变时;
c) 停产一年以上再恢复生产时;
d) 连续生产时每一年进行一次;
e) 出厂检验结果与上次有较大差异时。
8.3.2 型式检验应按表7、表8、表9规定的项目进行检验。
8.3.3 抽样与判定规则如下:
a) 片头、螺纹管口、丝堵、放气丝堵型式检验应按GB/T 2828.1规定的一般验收水平Ⅰ,采用正常抽样一次或二次抽样方案,检验项目接收质量限应符合表10、表11的规定。
b) 钢管型式检验从合格品中抽1‰进行检验,检查结果全部符合表8的规定,判定该批产品合格。
表10 片头检验抽样方案
表11 螺纹管口、丝堵、放气丝堵检验抽样方案
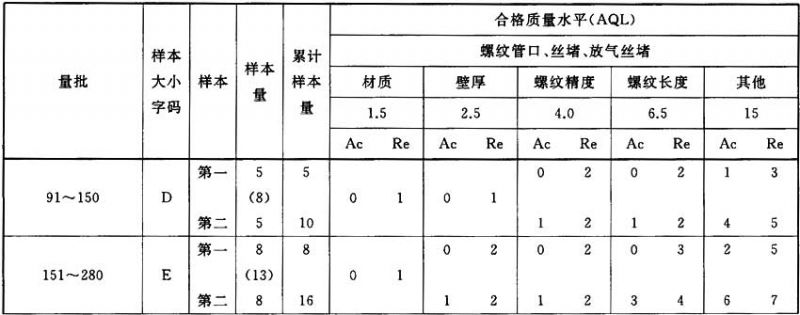

9 合格证、包装和贮运
9.1 合格证
产品出厂应附产品合格证,应至少包括如下内容:
a) 产品商标;
b) 制造厂名称和地址;
c) 产品名称及标记;
d) 出厂日期;
e) 产品执行标准编号。
9.2 包装
9.2.1 包装应采用能够保证产品在搬运装卸时不变形、不损伤产品质量的包装措施。
9.2.2 钢管的包装、标识及质量证明书应符合GB/T 2102的有关规定。
9.2.3 每捆钢管以钢质打包带捆扎,打包带内应衬纸板等保护垫层。
9.3 贮运
9.3.1 产品运输时应采取防雨措施。
9.3.2 在运输和搬运过程中应避免磕碰及其他重物挤压。
9.3.3 产品应存放在空气干燥的库房。